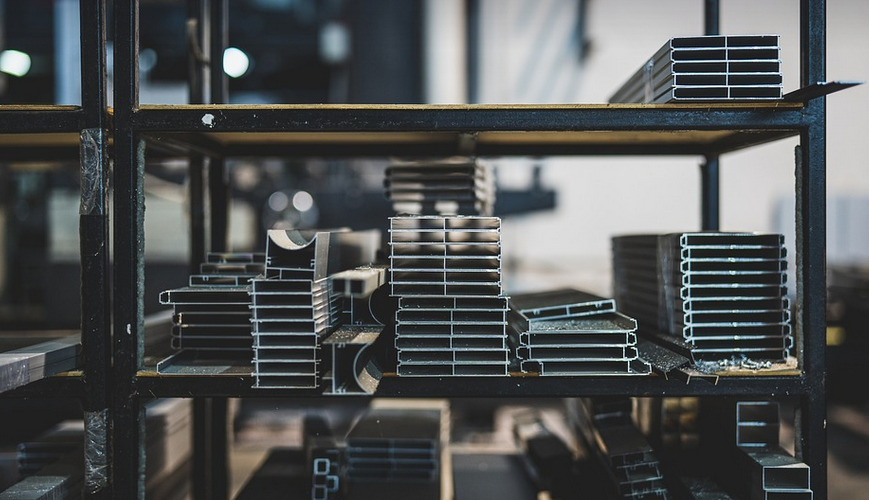
Understanding the Importance of 2/0 Welding Cables
In the world of electrical work, choosing the right cable is paramount to ensuring safety and optimal performance. When it comes to welding applications, especially those involving high amperages and demanding conditions, understanding the significance of 2/0 welding cables becomes essential.
As with most aspects of electrical engineering, there’s a reason behind the use of specific cable sizes and terminology. Welding cables are no different, as they require specialized materials and designs to handle the immense heat and currents responsible for powering welding processes.
What is 2/0 Welding Cable?
The term “2/0” refers to a specific gauge rating of electrical wire – an indication of its diameter. Specifically, a 2/0 cable means it has two-gauge wires (often referred to as AWG), each with a 7.0 mm or 0.28 inches in diameter.
This distinctive size signifies the cable’s ability to safely and effectively transport large amounts of electric current under high working temperatures, essential for welding operations.
It’s important to note that the thickness (or gauge) of a wire is directly linked to its electrical resistance. A larger diameter generally translates to lower resistance, enabling better flow of electricity and reducing heat dissipation.
Why Choose 2/0 Welding Cable?
Choosing the appropriate 2/0 welding cable for any application plays a pivotal role in both safety and efficiency. Here’s why:
**1. High Amperage Capacity:** 2/0 cables are designed to handle substantial amperages, which is crucial for demanding welding processes. The larger gauge facilitates the transfer of large amounts of current without resistance issues.
**2. Heat Resistance and Insulation:** Welding processes generate immense heat, and this necessitates high-quality cables that can withstand extreme temperatures. 2/0 cables are typically made with materials that resist degradation at high temperatures, ensuring safety.
**3. Durability and Longevity:** Welding cables undergo constant stress and wear from the heavy currents used in the process. A robust cable like a 2/0 welding cable contributes to longevity and reduced downtime for your equipment.
**4. Safety and Performance:** Choosing a suitable cable ensures proper function and prevents potential hazards associated with overloading circuits or faulty connections.
Selecting the Right 2/0 Welding Cable
Choosing the right 2/0 welding cable is not just about selecting a larger diameter – there are multiple factors to consider, including:
**1. Welding Process:** The type of welding determines the necessary amperage and current required. Different welding processes have specific needs.
**2. Voltage Rating:** The voltage rating of the cable is essential for ensuring compatibility with your welding equipment’s voltage source. A mismatch can cause electrical surges, potentially damaging the equipment or causing safety hazards.
**3. Wire Gauge and Insulation Type:** Choosing the correct insulation type is crucial for efficient heat dissipation. Some common insulation types include:
- **PVC (Polyvinyl Chloride):** Cost-effective, abrasion-resistant, and offers good electrical insulation
- **XLPE (crosslinked polyethylene):** Offers superior resistance to oil, chemicals, and extreme temperatures
- **HMWPE (high-molecular weight polyethylene):** High tensile strength, excellent corrosion resistance, and long service life
**4. Cable Length:** The length of the cable must be balanced with other factors. Consider the distance between the welding equipment and your source to avoid potential power loss due to cable resistance.
**5. Manufacturer Quality:** Ensure you choose reputable manufacturers offering high-quality cables, certified by relevant quality control organizations.
Safety Considerations for 2/0 Welding Cables
Working with electrical current can be extremely dangerous if proper precautions are not taken. Ensure your welding operation adheres to the following safety guidelines:
**1. Trained Personnel:** Only trained and qualified personnel should perform welding operations.
**2. Disconnect Power Before Handling Cables:** Ensure you disconnect the power before handling or installing cables. This prevents accidental shocks and other hazards.
**3. Secure Connections:** Use proper crimp connections to ensure secure connections, preventing wire chafing and potential electrical shorts that could lead to fire.
**4. Inspect Cables Regularly: **Ensure cables are inspected regularly for damage or wear. Damaged cables can cause safety hazards during operation.
**5. Electrical Safety Compliance:** Adhere to all relevant electrical codes and regulations when working with high-voltage welding applications.
Conclusion
2/0 welding cables are indispensable for safe and efficient welding operations. This article has provided a comprehensive overview of their significance, choosing the right cable, and safety considerations. Always prioritize safety and ensure your operation adheres to best practices when working with high-amperage current.
Remember that proper selection and installation of 2/0 welding cables contribute to the longevity of your equipment, as well as ensuring a safe working environment for yourself and others.