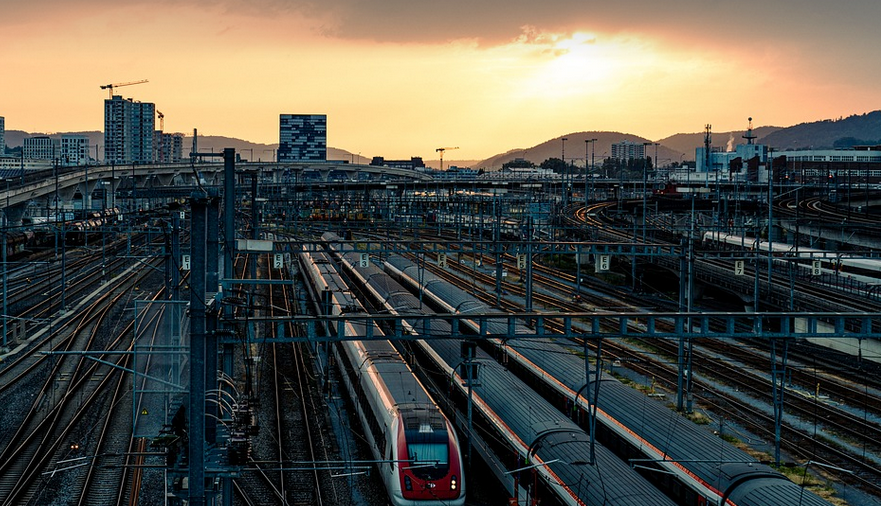
Understanding the Basics
Welding rods, those crucial ingredients in the metal magic of welding, come in a variety of compositions and applications. One such type is 308L-16 welding rod, often used for its versatility and robust performance in various projects. But what exactly does amperage have to do with this?
Think of amperage as the electric “flow” that fuels the welding process. Just like water flows through a pipeline, it needs the right amount of pressure and volume to make things happen. In welding, we need to maintain a stable flow of electricity to melt the metal and create a strong joint.
The 308L-16 welding rod, thanks to its composition (which we’ll discuss in detail later), requires specific amperage settings to work optimally. Too low, and the weld won’t be hot enough; too high, and you risk burning or damaging the materials.
Amperage is a critical factor in determining the heat input into the metal being welded. It directly impacts how fast the rods melt, how much heat builds up at the joint, and ultimately, how thick and strong the weld will be.
But why does amperage matter so much? Well, think of it as the right amount of energy pushing the welding torch through the metal. Too little, and you’ll struggle to create a proper connection. Too much, and you risk damaging the material or even melting it down.
For 308L-16 welding rod, finding the perfect amperage setting involves balancing several factors: the type of welding process, the thickness of the metals being joined, and how quickly the heat needs to be applied.
The 308L-16 Welding Rod: Composition and Amperage
Before delving into the specifics of amperage settings, it’s crucial to understand what makes 308L-16 welding rod unique. This type of rod is known for its strength, flexibility, and ability to resist high temperatures without compromising its integrity.
The composition of this rod plays a significant role in determining the optimal amperage setting. It’s crucial to understand that 308L-16 rods contain varying percentages of elements like chromium and nickel. These components directly influence the rod’s ability to conduct electricity and resist heat.
For example, higher chromium content translates into a stronger weld with less chance of deformation, while increased nickel improves its resistance to high temperatures.
Finding the correct amperage setting for 308L-16 welding rods requires careful consideration of these factors and a bit of trial and error based on your specific welding needs.
Remember, each welding project is different, so finding the perfect balance between amperage and material thickness will be key to achieving the desired weld strength and longevity.
Understanding Amperage Requirements
Let’s dive into some specifics about 308L-16 welding amp settings. We’ll look at the common ranges, highlighting the factors that influence these settings. Remember, it’s always best to consult your rod manufacturer for their specific recommendations.
For instance, when using 308L-16 rods for sheet metal welding, you might start with an amperage between 150-200 amps. This will provide a good weld quality and help prevent overheating.
As the thickness of the metals changes, so does the amp setting. If you’re welding thicker materials like steel plates, a higher amperage (around 250-300 amps) might be needed to ensure deeper penetration and better weld strength.
However, always remember that too high an amperage can lead to excessive heat and deformation of the metal being welded. It’s about finding the right balance.
For thick sections of steel plates, a higher amperage setting might be required. Experimenting with different amperage settings to achieve the desired weld quality is crucial for success.
The 308L-16 welding rod works best at moderate amperage levels, but always be conscious of your chosen material thickness and welding process.
It’s important to experiment to find the optimal amperage setting that achieves the desired weld quality without compromising the integrity of your material.
Factors Affecting Amperage Settings
Several factors influence the ideal amperage settings when working with 308L-16 welding rods:
Firstly, consider the welding process you’re using. TIG Welding, Shielded Metal Arc Welding (SMAW), and Gas Tungsten Arc Welding (GTAW) all have unique requirements regarding amps.
Secondly, always factor in your material thickness. Thicker materials need higher amperage settings to penetrate deeper and solidify the weld effectively.
Thirdly, remember that welding rod composition plays a role in determining amp setting. The 308L-16 rods are known for their strength and ability to resist high temperatures without compromising their structure.
Finally, consider your specific project’s requirements. Are you working with thin sheets or thick plates? What kind of metal are you welding? These factors will all influence the ideal amperage setting.
Always remember, finding the right balance is key to achieving a successful weld.
Final Thoughts
Mastering the art of amperage settings for 308L-16 welding rods requires understanding various elements like rod composition and welding processes. Experimentation and practice will ensure you find the optimal amp setting for each project.
With proper knowledge, you’ll be able to maximize your weld quality and create strong, long-lasting joints. Remember, always prioritize safety while welding, wear appropriate protective gear, and follow all recommended procedures.
Happy welding!