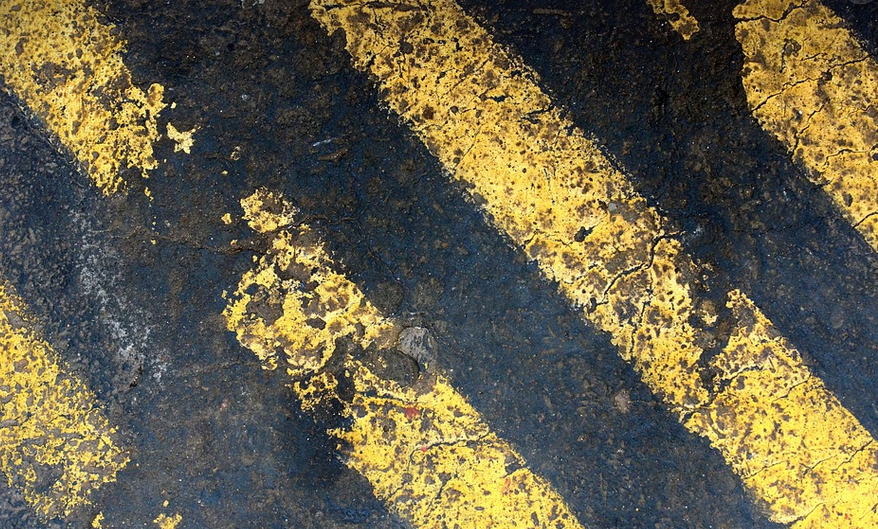
What Are Welding Rod Amps?
Imagine welding a steel beam, or maybe fixing that leaky fence post – those are tasks where you need to connect metal pieces together using heat and pressure. It’s not as simple as just holding two pieces of metal together; it needs controlled force and precise temperature for the best results. In this world of welding, understanding the role of “amps” is crucial.
Welding rods, those handy little metal sticks used to build up metal structures on a piece of equipment, are designed with specific characteristics that dictate how well they interact with welding machines. These characteristics include their diameter (which impacts the heat output), composition (affecting conductivity and weldability), and most importantly, their amperage.
Amps: The Power Behind the Welding Process
As a term in electronics, amps simply denotes “amperes.” It represents the flow of electric current through a circuit. When you think about it, every electrical device that powers up requires this flow in order to work – from your phone charging to the lights you use at night.
In welding, amps are what determine how much power is being delivered to the workpiece. Think of it like turning up or down the heat on a stove – higher amps mean more heat and vice versa. The ideal amperage for any specific welding rod depends heavily on the type of metal you’re working with and the desired outcome.
For instance, thicker steel sheets require more power to melt than thin ones, just like how a large pot in your kitchen needs more heat compared to a small one.
Why is Finding the Perfect Amp Setting Important?
Understanding the relationship between current and weld quality is crucial. Too much or too little amperage can lead to problems.
If you use a setting that’s too high, you risk burning through your metal workpiece. It can cause discoloration or even damage the material due to excessive heat.
On the other hand, if you dial in an excessively low amperage, your arc might struggle to melt the metal effectively, resulting in a weak weld with a poor finish. You’ll end up with some rust and corrosion, compromising the work’s quality
Finding Your Ideal Amp Setting
Determining the optimal welding rod amp setting involves considering several factors:
1. **Welding Process:** There are different welding processes to choose from, each with its unique requirements. For instance:
- **MIG (Metal Inert Gas):** This widely used process utilizes a wire electrode fed through the welding gun and shielding gas to create a weld pool.
- **TIG (Gas Tungsten Arc Welding):** This more precise process usually uses a non-consumable tungsten electrode, offering high control during the welding process. It’s known for producing high-quality welds on thinner materials.
- **Stick/SMAW (Shielded Metal Arc Welding):** The traditional stick welder uses an electrode coated with flux to create a weld pool. These welders are commonly used in industrial settings.
2. **Welding Position:** Welding position also plays a significant role. For instance:
- **Flat position:** Easier and faster to set the amps for welding flat or horizontal surfaces.
- **Overhead position:** Requires more skill and precision due to the challenge of working at an angle and maintaining consistent arc length
3. **Metal Type & Thickness:** The type of metal being welded can impact the ideal amp setting:
- **Steel:** Thicker steel sheets often require higher amps than thin pieces, due to their greater density.
- **Aluminum:** Aluminum tends to be a lighter and more easily weldable material. Setting the amperage lower might be optimal.
4. **Weld Size & Seam Type:** The size of the weld seam and its type also play a role in determining the optimal amp setting. For instance, thicker sections require higher amps for thicker weld seams.
The Importance of Using the Right Amp Setting
Choosing the right amperage is crucial throughout the welding process. Remember this: The right amount of power can influence the arc stability, weld penetration, and overall quality of your welds.
Experimenting with different amp settings will help you determine the ideal setting for your specific metal thickness, desired weld profile, and type of welding process.
How to Find Your Ideal Amp Setting
Finding the optimal amperage can be daunting; however, it’s necessary for a high-quality weld. Here’s how you can get started:
- **Consult your welder’s manual:** This will provide detailed information about recommended amp settings and welding parameters specific to your equipment.
- **Start with a lower amperage setting:** Begin by setting the amperage lower than a usual, you often need to adjust the settings up gradually.
- **Observe the weld puddle:** The weld pool should be fluid and free of inconsistencies. If it’s too small or too large, adjust the amperage as needed.
- **Test different amp settings:** Experiment with a range of amperages to find out what works best for your specific welding project and metal type.
By following these steps, you’ll be able to achieve consistent weld quality with greater control over the process. Remember, practice makes perfect!