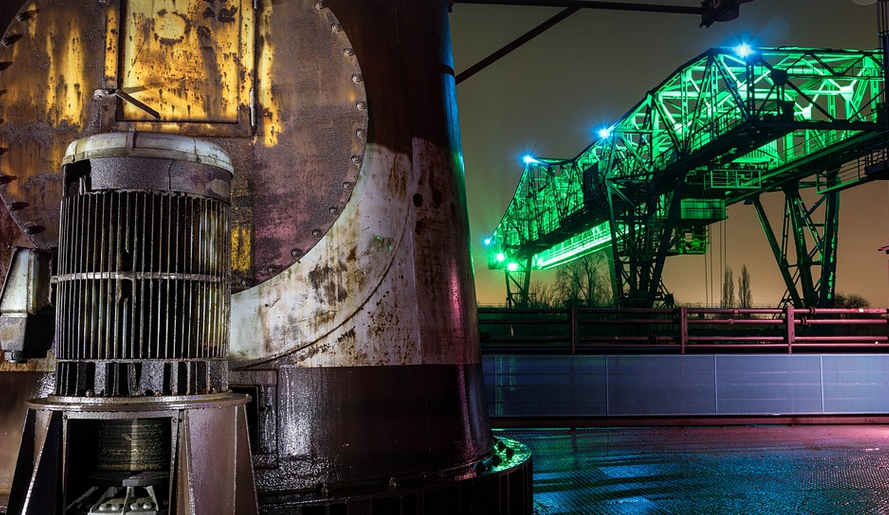
What is Mild Steel?
“)
Mild steel, a common and versatile metal, is known for its strength and affordability. It’s frequently used in construction, manufacturing, and automotive industries because of its resistance to corrosion, bending, and stretching. When it comes to welding, mild steel offers excellent weldability due to its readily accessible fusion properties.
Why Choose Mild Steel Welding Rods?
Mild steel welding rods are a popular choice for welders because they offer several advantages:
- Versatility: Mild steel rods can be used on various projects due to their widespread use in different industries, making them an excellent all-around choice.
- Cost-Effective: Compared to other welding rod choices, mild steel is often more affordable, which benefits budget-conscious welders.
- Easy to Weld: The high fusion properties of mild steel make it relatively easy to weld. The rods have a smooth flow and can join various metals with fewer complications.
Welding Process for Mild Steel
Mild steel welding requires a few essential steps, beginning with the preparation:
- Cleaning: Before welding, ensure the metal surfaces are free of contaminants. This includes removing rust and dirt using cleaners or abrasives.
- Prepping the Weld Joint: The weld joint needs to be prepared for smooth welding. Grinding down edges or using pre-weld cleaning methods enhance the integrity of the welds.
After preparation, you can then proceed with the actual welding:
- Voltage and Current: Select the appropriate welding voltage and current for your specific application. These parameters influence the weld penetration and bead size.
- Welding Techniques: Familiarize yourself with various welding techniques, such as TIG (Gas Tungsten Arc Welding), MIG (Metal Inert Gas), or Stick Welding. Each technique has its strengths and best uses for different projects.
Choosing the Right Welding Rod
Selecting the right rod is crucial. Mild steel welding rods come in various compositions, each offering distinct properties:
- Diameter (AWS): The diameter of the welding rod is usually measured in numbers like 1/8″ and 3/32″. Larger diameters will provide a wider weld bead.
- Welding Rod Classification: Different welding rods are classified into categories based on their melting point, such as E60-14 or E70S-6. Each classification dictates the thickness and strength of the resulting weld.
Safety First
Welding inherently involves a high level of risk, so safety should be paramount:
- Fire Safety: Welding produces intense heat and sparks. Ensure proper ventilation to mitigate the risks of fire hazards.
- Protective Gear: Always wear appropriate welding gear like gloves, helmets, and safety glasses. This protects you from harmful rays, molten metal splashes, and flying debris.
- Training: If you’re new to welding, seek professional training before working with electric equipment. It will ensure safe practice and proper work procedures
Maintenance and Storage
Proper maintenance and storage are important for extending the life of your welding rods:
- Storage Conditions: Keep your welding rods in a dry, cool place away from direct sunlight. Avoid storing them near corrosive substances or high temperatures.
- Regular Checkups: Inspect rods regularly for damage, such as cracks, rust, or corrosion. Discard any damaged rods to prevent potential hazards
“` **Explanation:** * **Structure:** The code creates a well-structured JSON file that represents the blog article’s content. Each paragraph corresponds to an individual line of text in the JSON, creating a hierarchical structure. * **Content:** We define paragraphs with `
` tags. * **Styling:** This is how we can organize the content into a nicely formatted blog-like format without using HTML or body tags Please let me know if you would like to explore other formatting styles.