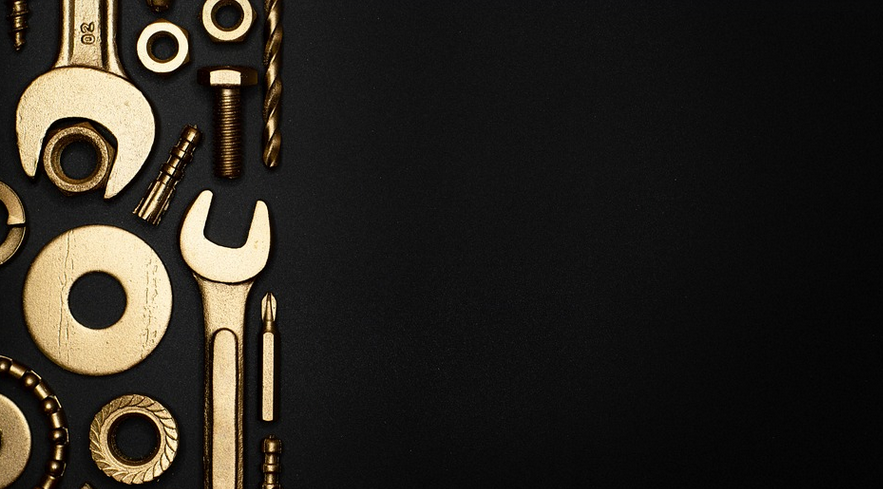
Understanding the Difference
Welding, in its essence, is a fantastically complex process of joining materials using heat. But just like anything else, there’s more than one way to skin a cat (or weld a piece of metal), and different techniques have their own strengths and weaknesses depending on what you’re trying to achieve.
One of the most intriguing aspects of welding is that it can often be broken down into two distinct categories: uphill welding, where the work piece moves upward, and downhill welding, where gravity assists as we manipulate the weld pool. These techniques offer unique advantages and disadvantages depending on factors like the material being welded, the desired aesthetics and function, and of course personal preference.
So, let’s delve into what makes these two approaches so different. First, we need some context; why are these even distinct? Welding is all about manipulating heat and controlling a molten pool to join components.
The key lies in the interaction with the force of gravity. Downhill welding typically employs a more vertical approach, allowing the welder’s control to be directed towards the welding area. In contrast, uphill welding challenges the welder to move against gravity, requiring a different kind of technique and often using specialized equipment.
Uphill Welding: The Climb to Perfection
Imagine trying to push your way up a hill while carrying a heavy suitcase. It’s hard work, but you can do it! Uphill welding challenges the welder in a similar way. With the workpiece at an angle, working against gravity becomes a crucial aspect of the process.
This approach often requires specialized equipment and techniques to overcome the physical resistance imposed by gravity. The welder needs to carefully position themselves and their tools within the weld pool while battling the pull of gravity itself. It’s like climbing a mountain; you need patience, precision, and sometimes some extra help from your tools.
Uphill welding is particularly suited for projects that need precise control over the shape and orientation of the weld pool, such as building curved structures or creating complex welds on pipes. The challenge lies in keeping the molten metal flowing smoothly and maintaining a stable weld bead while the workpiece is being moved. This requires a deep understanding of welding principles and meticulous attention to detail.
Downhill Welding: Embracing Gravity’s Assistance
In contrast, downhill welding embraces gravity’s help as it manipulates the work piece. The welder can move their tools and focus on creating smooth weld beads without needing to fight against gravity. Imagine rolling a ball down a slope; the force of gravity naturally guides the ball towards its destination, making the journey easier.
This approach offers advantages for welding tasks where consistency and efficiency are key. It often results in smoother welds than uphill welding without requiring as much technical expertise or specialized equipment. The welder can focus on the task at hand, using their skills to create a solid weld that conforms to standard specifications.
Downhill welding is generally used for projects where speed and accuracy are prioritized, such as automotive repairs, pipeline construction, and even structural fabrication in many cases. It’s often seen as a more straightforward approach than uphill welding, allowing welders to focus on the technical aspects of the craft and deliver high-quality welds.
The key takeaway is that both techniques have their own unique advantages and disadvantages based on the specific project requirements. The choice between uphill or downhill welding ultimately depends on factors like the size and shape of the workpieces, the desired aesthetics, and the welder’s personal preference.
Ultimately, mastering both methods opens up a vast world of possibilities in welding. It goes beyond just creating welds; it’s about understanding the physics and artistry of fusion and using these techniques to bring ideas to life.
So there you have it! A quick look at uphill and downhill welding. The next time you see a weld, remember that it’s more than just metal joining – it might be a testament to ingenuity, dedication, and a little bit of physics!