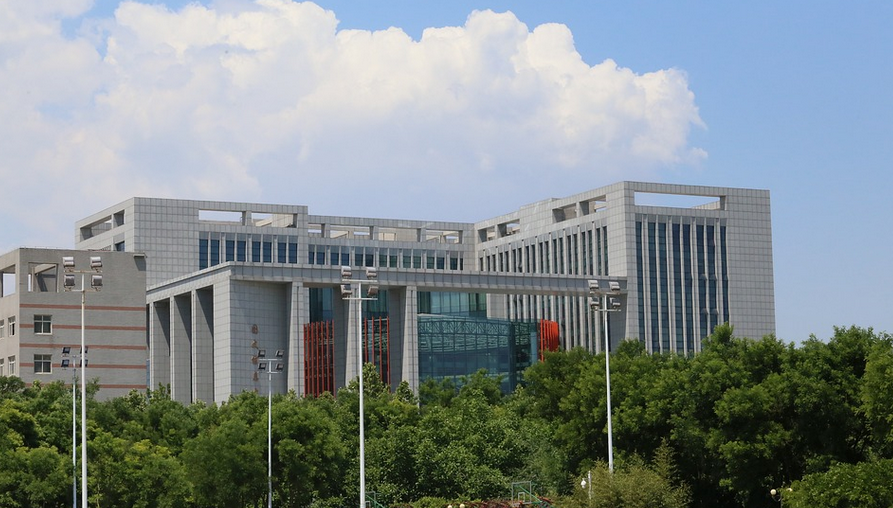
What is Hard Face Welding Wire?
Let’s face it, welding is about more than just sticking metal together—it’s about creating solid, durable connections that can withstand real-world pressure. That’s where hard face welding wire comes in. This special type of wire is designed to handle the most challenging environments and tasks.
Imagine you need to tackle a project involving harsh chemicals, extreme temperatures, or even corrosive materials. Traditional welding wires just won’t cut it; they’ll be corroded away or just plain melt down under pressure. That’s where hard face welding wire shines. It boasts a unique composition that allows it to withstand these sorts of harsh conditions while delivering exceptional welds.
Unveiling the Secrets: What Makes Hard Face Welding Wire Special?
Hard face welding wires are known for their remarkable resistance to abrasion, wear and tear, and even extreme temperatures. This is achieved through a combination of unique additions to the wire’s composition:
**1. Reinforced Metal Particles:** These microscopic particles are strategically incorporated into the wire structure. Their presence strengthens the wire, making it much more capable of handling high-stress situations and prolonged use.
**2. High-Quality Alloys:** The very foundation of hard face welding wire is built upon a blend of high-quality alloys that are specifically engineered to resist wear and tear. These alloys not only enhance the welding process but also provide lasting resistance against corrosion, thus extending the lifespan of your weld.
**3. Specialized Coating:** A protective coating can be applied to hard face wire for added protection. This coating acts as a barrier against moisture, corrosive elements, and other damaging factors. It’s like adding an extra layer of armor to the wire itself!
Benefits You Can’t Ignore: Why Choose Hard Face Welding Wire?
Hard face welding wire opens doors to new possibilities in various welding applications:
**1. Improved Weld Quality:** With hard face wires, you’ll enjoy smoother, more consistent welds with a higher quality finish. This is because the wire resists deformation and wear, allowing for sharper edges and cleaner seams.
**2. Increased Durability:** Hard face welding wires are built to last! Their resistance to abrasion makes them ideal for demanding projects where longevity is paramount. They can withstand the rigors of heavy-duty use without compromising their performance.
**3. Wider Welding Range:** Hard face wire works in a variety of applications, from high-temperature welding jobs to challenging industrial environments. This versatility allows you to tackle projects across different industries with ease.
Choosing the Right Wire: What Every Welder Needs to Know
Selecting the right hard face wire for your specific welding task is crucial. It requires considering several factors:
**1. Material:** The type of metal being welded will influence the choice of wire. For instance, if you’re working with stainless steel, you might need a wire formulated specifically to handle its unique properties.
**2. Welding Process:** Different welding processes have specific requirements for the type of wire to be used. For example, TIG welding usually calls for different materials than MIG.
**3. Weld Joint Configuration:** The shape and size of the weld joint will also dictate the best choice. For instance, a thicker seam might require heavier-duty wires with higher tensile strength to ensure a secure and lasting weld.
Applications that Demand Hard Face Wire: Pushing Boundaries in Various Industries
Hard face welding wire is finding its way into an increasing number of industries due to the impressive versatility it offers:
**1. Automotive Industry:** Automotive factories utilize hard face wire extensively for repairs and fabrication, where high-strength weldments are needed in demanding conditions.
**2. Aerospace Industry:** From aircraft repair to space exploration, the aerospace industry benefits from robust welds created with hard face wire. The wires’ resistance to extreme temperatures and pressure is a vital asset for these critical applications.
**3. Chemical and Petrochemical Industries:** These industries often work with harsh chemicals and corrosive environments, demanding welding wires that can withstand the challenges posed by their specific work conditions. Hard face wire fulfills this need effectively.
Future Trends: The Evolution of Hard Face Welding Wire
The future of hard face welding wire holds exciting possibilities. As technology advances, so will the development and application of this essential material:
**1. Enhanced Performance:** Scientists continue to explore new materials and alloys that can further enhance the strength, conductivity, and durability of hard face wires.
**2. Smart Welding Techniques:** New welding techniques, such as laser welding and friction stir welding, are becoming more prevalent. These advancements rely on specialized wires designed to work effectively with these intricate processes.
**3. Sustainable Solutions:** The focus is shifting towards sustainable manufacturing practices. Research into eco-friendly materials for hard face wire will continue, aiming to minimize environmental impact while maintaining performance and durability.