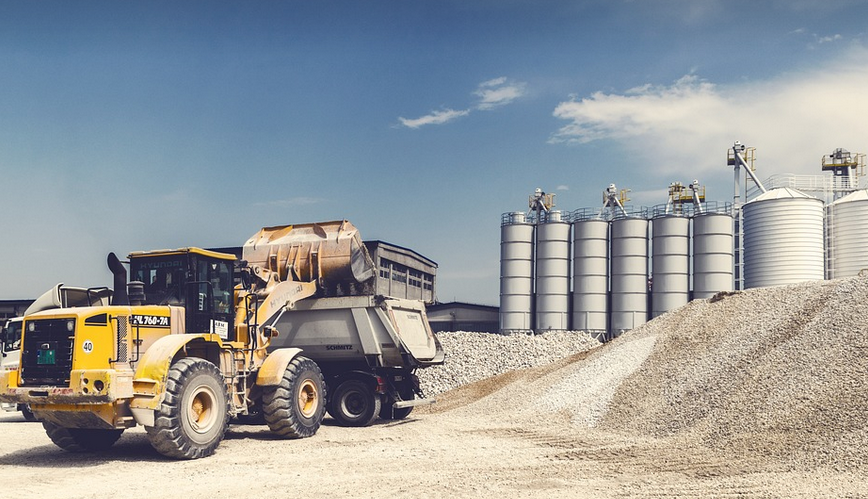
Understanding the Basics
Welding 1/4 steel, also known as mild steel, is a versatile and popular skill in various industries. Whether you’re a DIY enthusiast, an aspiring welder, or a professional tradesperson, mastering this art can unlock countless opportunities for creating robust structures and repairs. This guide will explore the fundamentals of welding 1/4 steel in 2024, providing insights into techniques, safety considerations, and helpful tips for achieving successful welding.
What is 1/4 Steel?
1/4 steel refers to a type of mild steel commonly used for various applications. This material possesses good weldability due to its composition and relatively low cost. It is often chosen for projects requiring structural integrity, like building frames, fences, gates, machinery components, and agricultural equipment. The “1/4” denotes the thickness of the steel sheet, which typically ranges from 0.063 inches to 0.25 inches.
Choosing the Right Welding Technique
There are several welding techniques for 1/4 steel, each with its own pros and cons:
- **Shielded Metal Arc Welding (SMAW):** Also known as “stick welding,” this technique uses an electrode coated in flux to create a weld pool. It’s relatively simple to learn but requires more practice for precise control. Its portability makes it ideal for on-site work and small projects.
- **Gas Metal Arc Welding (GMAW):** This method employs a continuous wire electrode fed through a welding gun, creating a weld pool in the process. GMAW offers high deposition rates and is well-suited for larger projects requiring speed and precision.
- **Gas Tungsten Arc Welding (GTAW):** Also known as “TIG” welding, this technique uses a non-consumable tungsten electrode to create an arc between it and the workpiece. It provides high quality welds with excellent control over heat input, making it suitable for intricate jobs requiring precision.
Essential Safety Precautions
Welding is inherently a potentially hazardous activity. Prioritize safety at all times by following these crucial steps:
- **Personal Protective Equipment (PPE):** Always wear appropriate PPE, including welding helmets, gloves, and protective clothing, to shield your face, hands, and body from harmful sparks, radiation, and fumes.
- **Ventilation:** Ensure adequate ventilation in the workspace by opening windows or using fans to prevent the buildup of hazardous gasses.
- **Grounding:** Ground your welding equipment to the workpiece to avoid electrical shocks.
- **Fire Safety:** Keep a fire extinguisher within reach and be mindful of flammable materials in the vicinity.
- **Training:** Seek professional training from qualified instructors before working with welding equipment, especially if you’re new to the field.
The Welding Process: Step-by-Step
Welding 1/4 steel requires a precise and systematic approach. Here’s a simplified breakdown of the process:
- **Prepare the workpieces:** Clean both surfaces thoroughly to remove dirt, rust, oil, and any scale before welding.
- **Select your electrode/wire:** Choose the correct electrode diameter based on the thickness of the steel and desired welding type.
- **Set up the welding machine:** Connect the appropriate wire feeder, shielding gas (if required), and select the welding parameters (current, voltage, travel speed) for optimal weld quality.
- **Position the workpieces:** Ensure they are positioned correctly in the welding position to allow access for the welding torch.
- **Start welding:** Adjust the welding parameters as needed and begin welding the joint, using smooth movements with controlled speed.
- **Complete welding:** Finish welding to achieve a complete fusion of the metal surfaces.
- **Post-weld inspection:** Check for any defects like porosity or under-fill in the weld pool before finishing.
Welding 1/4 Steel: Tips and Tricks
Here are some valuable tips to enhance your welding skills:
- **Practice makes perfect:** Always start with basic practice welds to develop muscle memory, control, and technique.
- **Start small:** Begin with thin sheets of steel before moving onto thicker materials to gain confidence and familiarize yourself with the process.
- **Keep your electrode clean:** Ensure a clean electrode tip for optimal penetration and consistent weld quality.
- **Pre-heat the workpiece:** If required, preheating the steel can help reduce distortion and improve weld penetration in some applications.
- **Use proper shielding gas:** When using MIG welding, use a shielding gas to protect the weld pool from atmospheric contaminants.
- **Don’t rush through the process:** Take your time for each step; rushing can lead to inconsistent welds and potential defects.
Looking Ahead: The Future of Welding
Welding technology continues to evolve with advancements in materials, automation, and digitalization. Here are some key trends shaping the future of welding:
- **Automated welding:** Robots and automated systems will play a bigger role in manufacturing and industrial welding applications.
- **Laser welding:** Laser welding offers highly precise control, minimal distortion, and rapid production rates, opening up new possibilities for various industries.
- **Additive manufacturing (3D printing):** Welding will become increasingly integrated with additive manufacturing techniques to combine material deposition and structural design in complex assemblies.
Conclusion: Embrace the Challenge
Welding 1/4 steel is a rewarding skill that opens doors for various career paths. Remember, like any craft, mastering it requires patience, practice, and dedication. By embracing quality techniques, adhering to safety protocols, and staying updated on evolving trends, you can unlock your welding potential and contribute to building a better future.