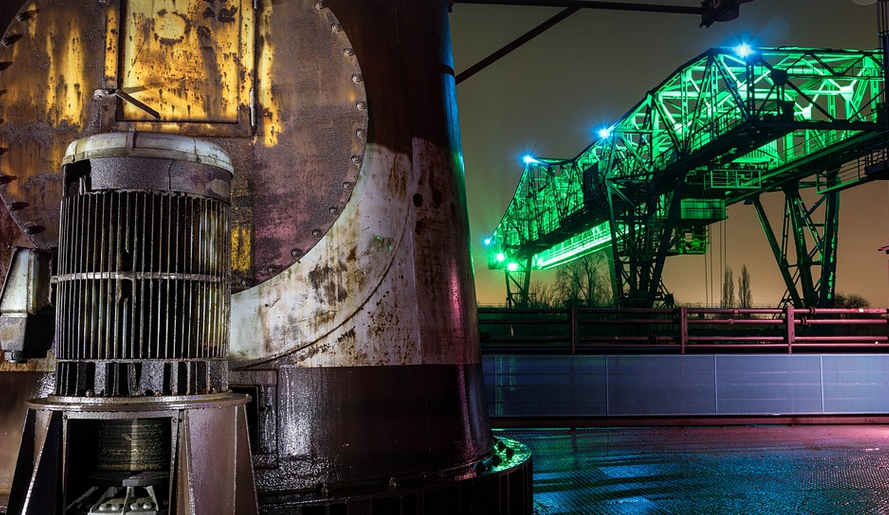
The Need for a Roll Cage: Safety First, Then Freedom
There’s a thrill in pushing the limits of your vehicle. Whether you’re traversing rugged terrains, tackling challenging jumps, or simply cruising down dusty roads, there’s something undeniably liberating about hitting the open road. But as you take those adventures further into uncharted territory, safety becomes paramount. That’s where a roll cage comes in, serving not only as a structural reinforcement but also as a crucial piece of protection for you and your passengers. A roll cage is more than just a fancy enclosure; it’s the backbone of your off-road vehicle’s safety system. It provides an additional layer of stability and protection during high-speed maneuvers or sudden impacts, acting like a protective cage around the car’s structure. These cages are meticulously crafted with heavy-gauge steel sections welded together to form a rigid frame that can withstand extreme forces.
Why Tig Welding: The Art of Precise Strength
When it comes to constructing a roll cage, welding plays a vital role. TIG welding is often the preferred choice for this specific application due to its unique characteristics and advantages. TIG welding stands for “Gas Tungsten Arc Welding,” using a non-consumable tungsten electrode as the source of heat. This process allows for high precision and control over the welding parameters, resulting in welds that are strong and durable. Here’s why TIG is often the go-to choice for roll cage construction: * **Minimal Heat Distortion:** TIG welding provides minimal heat distortion to the metal being joined, ensuring less warping or deformation of the welded sections throughout the process. This is crucial for achieving a seamless connection that will hold up under pressure. * **Clean and Precise Joints:** TIG welding results in weld beads with exceptional cleanliness and precision, offering strong bonds and minimizing gaps between the metal pieces. This meticulous approach ensures that the roll cage’s structural integrity is maintained and enhanced. * **Enhanced Corrosion Resistance:** The use of inert gas shielding during TIG welding protects the weld area from atmospheric contamination, significantly reducing corrosion risks. This helps to maintain the integrity of your roll cage for years to come.
Tig Welding Roll Cages: A Closer Look at the Process
Welding a roll cage is more than just bolting things together; it’s about understanding the specific needs and challenges that come with creating a safe and durable structure for your vehicle. Let’s dive into the steps involved in constructing a roll cage using TIG welding: 1. **Planning & Design:** It all starts with meticulous planning, taking into account factors like the vehicle’s build, intended use (rally racing, off-roading, etc.), and desired level of safety standards. This initial stage involves creating a detailed blueprint that specifies the exact positions of each welded section, ensuring every piece is precisely integrated to create a robust cage 2. **Metal Selection:** The choice of metal plays an important role in the entire project. High-strength steel alloys are commonly used for roll cage construction due to their ability to withstand extreme forces and potential impacts. 3. **Welding Preparation:** The welding process begins with meticulous preparation. This includes cleaning the welded surfaces, removing any rust or impurities, ensuring that the metal is free from contaminants. 4. **TIG Welding Process:** The TIG welding process comes into play here. A skilled welder uses a TIG torch to melt and join the metal pieces together. It’s often done in stages, working with different sections of the cage before moving on to connect them. 5. **Quality Control & Finishing:** Every weld pass is carefully inspected for quality and integrity, ensuring that each connection meets the specific requirements. The final stage involves grinding down any rough edges and applying protective coatings.
Tig Welding Roll Cages: More Than Just Metal
The process of building a TIG welded roll cage goes beyond just technical expertise; it’s about understanding the intricate balance between safety, performance, and aesthetics. A well-built roll cage is not only a structural necessity but also an extension of your off-road personality.
Think of it as the heart and soul of your vehicle, where strength meets design, and each weld becomes a testament to a passion for adventure. For those seeking unmatched safety and durability while pushing their vehicles’ limits, TIG welding roll cages offer the perfect solution. Let’s explore how this process can be tailored to fit your unique off-road needs and aspirations.
The journey begins with a clear vision – an off-roader who craves adventure and wants to experience the thrill of the open road without compromising safety. A TIG welded roll cage becomes more than just a piece of equipment; it’s a symbol of that commitment to pushing boundaries, exploring new frontiers, and embracing the freedom of the open highway.