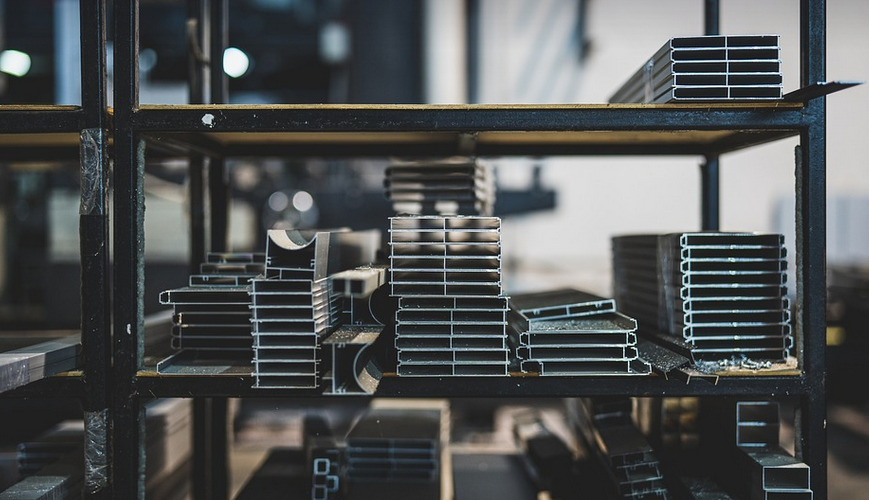
A Controlled Explosion for Precision Metalwork
Welding aluminum is a fascinating blend of art and science, requiring precise control over heat and airflow to achieve beautiful, strong joints. At the heart of this process lies the oxyacetylene flame, a powerful yet versatile tool capable of melting aluminum like molten glass. It’s not as complicated as it sounds; understanding this unique combustion process is key to mastering aluminum welding.
The magic of the oxyacetylene flame rests in its ability to produce a high-intensity, focused heat source. This localized intensity allows for intricate welding techniques that would be impossible with other methods. This is why it’s often considered the “gold standard” for welding aluminum, particularly in applications demanding strength and precision.
The process starts with a carefully controlled mixture of oxygen and acetylene gas, typically delivered to a specialized torch via separate hoses. The oxygen acts as an oxidizer, while the acetylene fuels the flame’s intense heat and produces a bright yellow color. This combination generates a highly reactive environment, ideal for melting aluminum.
When you ignite the mixture within the torch, the resulting flame undergoes combustion, producing energy in the form of light and hot gases. The concentrated heat from this controlled explosion melts the aluminum’s surface, allowing it to fuse with other metal pieces or create intricate joints. The oxyacetylene flame’s precise manipulation allows for precise control over the welding process.
The torch itself is an essential component of the welding process. It houses a carefully designed nozzle that directs the intense heat and airflow towards the aluminum surface, ensuring accurate melting and efficient welding. The shape and size of the nozzle are meticulously engineered to optimize the flame’s power and ensure precise control over its direction.
To master the oxyacetylene flame for aluminum welding, it’s crucial to understand and practice fundamental principles such as flame control, shielding, and heat input. These factors play a significant role in achieving consistent results and preventing damage to the workpiece or surrounding areas. It takes time to develop this expertise but the rewards are worth the effort.
One of the most important aspects of welding aluminum with an oxyacetylene flame is understanding how the flame’s characteristics affect melting behavior. The intensity, size, and direction of the flame all influence how it interacts with the metal’s surface. This knowledge allows you to manipulate the flame for precise control over the weld pool, ensuring a strong, clean joint.
For example, when welding aluminum on a thicker sheet, you may need to use a larger-diameter nozzle and adjust your torch angle to ensure even heat distribution across the entire sheet. This controlled manipulation ensures that the molten metal doesn’t overheat or burn through the workpiece. It also minimizes defects like porosity – holes in the weld that compromise the structural integrity of the aluminum piece.
The oxyacetylene flame comes with its own set of safety considerations, requiring a specialized knowledge and awareness. It’s essential to learn how to use the equipment safely, understand the risks involved, and follow proper safety procedures at all times. This includes wearing appropriate protective gear, practicing safe handling techniques, and using the equipment only in well-ventilated areas.
Remember, welding with an oxyacetylene flame is a complex process that demands a deep understanding of the technology and meticulous attention to detail. It’s not just about connecting metal; it’s about achieving precision and control through this unique combustion process. With practice, dedication, and the right knowledge, you can harness the power of the oxyacetylene flame for beautiful and lasting aluminum welding.