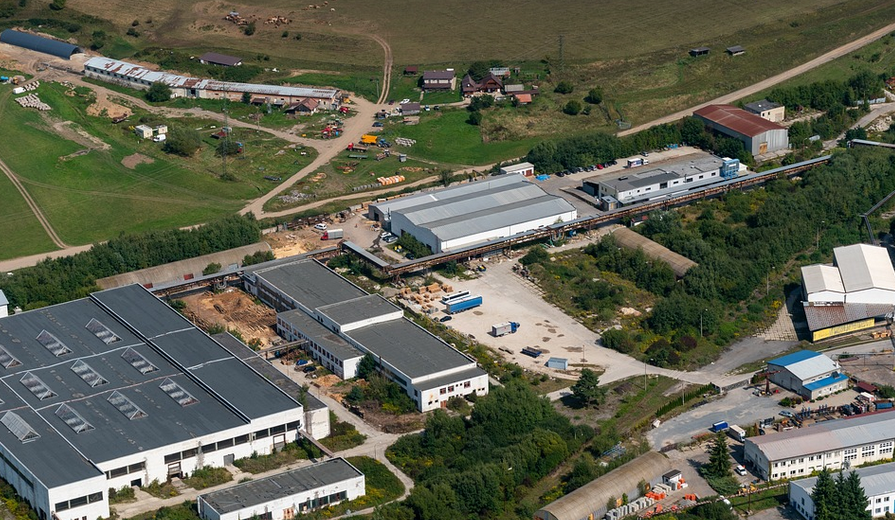
Understanding the Basics of 70S-6
When it comes to welding wire, there’s a whole world of choices out there. But for many welders and metalworkers, 70S-6 has been a stalwart in their arsenal, known for its versatility and reliability. But what exactly makes this wire so special? Let’s take a closer look at the 70S-6 formula.
The Chemistry of Weldability
70S-6 welding wire, as its name suggests, is built around a blend of materials that work together to create a weld with exceptional strength and durability. The key ingredient is “high carbon steel,” the backbone of many welding wires. This material provides the base for the wire’s structural integrity.
But 70S-6 isn’t just about the basic ingredients. Its success lies in the precise crafting of those materials. Engineers have carefully designed the composition to create a balance between strength, weldability, and cost-effectiveness. It’s this careful mix that allows welders to achieve high quality welds with minimal effort.
One of the most significant features of 70S-6 is its use of “filler metal.” Filler metal is crucial for welding. This material melts into the base metals, creating a smooth and strong weld pool that fuses the materials together.
The Power in Small Package
Now, let’s get to the heart of 70S-6’s magic – its small diameter and high-strength nature. With its tight weave and minimal weight, 70S-6 is incredibly versatile for various welding tasks, from thin sheets to thick structures.
Think about it this way: Imagine trying to weld a delicate piece of metal using a thick wire that’s hard to maneuver. It would be a challenge! But with 70S-6, the smaller diameter allows for easier penetration and smoother welds. This is especially important when dealing with tight spaces or intricate shapes.
The high-strength nature of 70S-6 also contributes significantly to its overall performance. This wire’s ability to resist deformation and stretch under pressure translates into incredibly robust welds, making it ideal for various demanding applications.
Unveiling the Advantages
So why has 70S-6 become such a popular choice? Let’s delve deeper into its benefits:
- Versatility: 70S-6 excels in welding various metals, including steel, cast iron, and stainless steel.
- Cost-Effective: It offers a balance between performance and cost, making it accessible for both beginners and professionals.
- Ease of Use: The smaller diameter makes it easier to handle and maneuver.
- Weld Quality: The tight weave and high strength result in smooth, durable welds with minimal effort.
- Wide Range of Applications: From automotive repairs and construction projects to fabrication and manufacturing, 70S-6 can tackle a wide range of projects.
Embracing the Future of Welding
While 70S-6 remains a popular choice for welding enthusiasts and professionals alike, it also signifies a shift towards more efficient and environmentally friendly practices in the industry. As technology advances, we can expect even more innovative welding wires to emerge, offering improved performance, reduced environmental impact, and enhanced safety.
So, when you’re considering 70S-6, remember that it’s not just about a specific wire. It represents a legacy of quality, reliability, and versatility in the world of welding. As a testament to its enduring legacy, 70S-6 continues to hold a prominent place within the hearts and minds of welders worldwide.