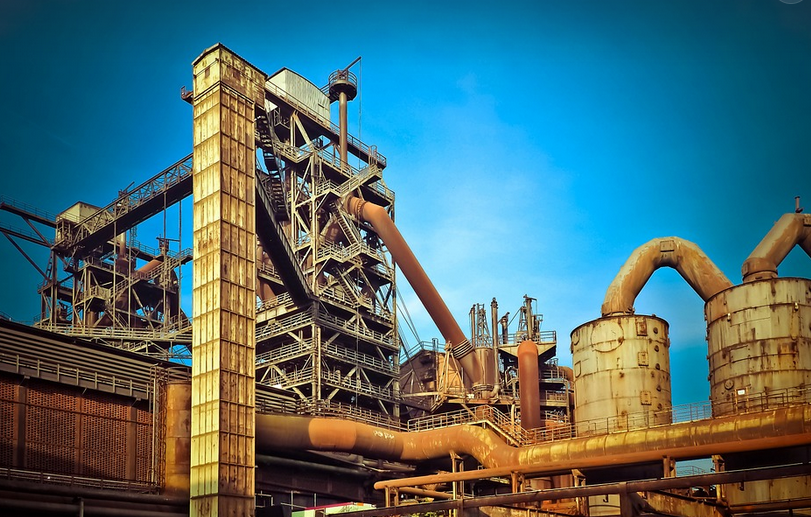
Understanding the Challenge
Welding cast iron and silicon bronze together can be tricky, even for seasoned welders. Cast iron is known for its exceptional strength and wear resistance, but it’s also notoriously difficult to weld due to its high carbon content and intricate grain structure. On the other hand, silicon bronze exhibits remarkable corrosion resistance and ductility, making it a popular choice for marine and industrial applications. However, these contrasting properties can create significant challenges when welding them together. Let’s delve deeper into the reasons behind this welding challenge:
Cast iron is notoriously difficult to weld due to its high carbon content and intricate grain structure. This makes it prone to cracking and distortion during the welding process. The high carbon content creates a very hard material, causing the heat from the arc to be absorbed more easily, leading to increased potential for warping or even outright failure.
Silicon bronze is a relatively soft metal compared to cast iron. But this very softness can lead to problems when you’re welding it. The molten metal in the weld puddle will flow readily, leading to potential porosity (holes) and undercut if not managed properly.
Adding to the complexity of this combination, heat-affected zones (HAZ), where the base metals change temperature during welding, are often complex for both materials. The HAZ can be quite large for cast iron in general and more so when dealing with silicon bronze, as its melting point is considerably lower.
Key Considerations for Success
Welding cast iron and silicon bronze successfully requires a comprehensive understanding of the inherent challenges these materials pose. Some crucial factors to consider include:
– **Arc Welding Technique:** The traditional arc welding methods like Shielded Metal Arc Welding (SMAW) or Gas Metal Arc Welding (GMAW) might not be sufficient for cast iron and silicon bronze due to their differing properties. TIG welding, known for its precision control and ability to focus on intricate details, proves to be a much better choice.
– **Weld Preprocessing:** Proper preparation is essential for any successful weld. For cast iron, preheating can help reduce the risk of cracking, as the material softens and becomes easier to manipulate during welding. However, preheating with silicon bronze needs careful consideration. It’s best to check if preheating could create stress in the material.
– **Filler Metal Selection:** Choosing the right filler metal is crucial. A filler metal designed for cast iron alloys can help bridge the gap between the materials and provide a strong, durable weld. There are specialized filler metals that can be used to join both materials effectively.
– **Welding Parameters:** Precise control over welding parameters like amperage, voltage, travel speed, and shielding gas flow is vital. The correct settings can help you minimize the chances of porosity and undercut while producing a strong weld in this challenging combination.
TIG Welding for Cast Iron and Silicon Bronze
TIG (Gas Tungsten Arc Welding) offers numerous advantages when working with cast iron and silicon bronze:
– **Precise Control:** The inherent precision of TIG welding makes it ideal for intricate work. It allows for precise control over the arc, leading to smaller weld beads, less distortion, and reduced porosity. The lower heat input provided by TIG minimizes the risk of warping or cracking.
– **Minimized Distortion:** TIG welding creates a small, controlled weld bead with minimal distortion, reducing the chances of significant shape changes and ensuring a smooth welding process.
– **Reduced Porosity:** The precision control over the arc allows for a clean melt pool, minimizing the formation of porosity. This is crucial in preventing potential cracks and failures that could occur due to trapped gases within the weld.
Steps for Successful TIG Welding:
Here is a simplified breakdown of the steps involved in welding cast iron and silicon bronze using TIG welding:
1. **Prepare the Components:** Clean both surfaces thoroughly, remove any rust or scale, and ensure that there are no gaps between the components.
2. **Preheating:** Preheat the materials to the recommended temperature for cast iron (around 70 degrees Celsius) before welding. This helps reduce the chances of cracking during welding.
3. **TIG Welding:** Use a TIG torch with an argon or helium shielding gas to protect the weld pool from atmospheric contaminants and ensure proper penetration.
4. **Welding Technique:** Start by making small welds (small beads) along the line of joining, gradually increasing the size as needed and checking for porosity in each stage of welding.
5. **Post-Weld Treatment:** Apply a final treatment to solidify the weld after welding using methods like annealing, which can help remove internal stresses and improve fatigue resistance.
Welding Tips for Success
Here are some valuable tips to maximize your success when welding cast iron and silicon bronze:
– **Practice:** Start with practice welds on scrap metal to master the technique before working on full-size components. This helps gain understanding of weld parameters, travel speed, and filler material selection.
– **Cleanliness is Key:** Ensure no debris or contaminants like rust or oil are present on the welding surfaces as this can interfere with the flow of filler metal.
– **Proper Ventilation:** Since TIG welding involves gas shielding and argon or helium, ensure proper ventilation to remove the fumes generated during welding.
– **Safety First:** Always wear appropriate safety gear like welding helmets and gloves to protect yourself from sparks, heat, and potential hazards.
The Importance of Proper Maintenance
Even with meticulous planning and execution, maintaining proper equipment is crucial for any welding job. This can help ensure longevity and optimal performance throughout the project’s lifespan:
* **Regular Cleaning:** Regularly clean your TIG torch tips and electrode holders to prevent build-up of contaminants that could impact weld quality. * **Gas Purity:** Maintain high-quality shielding gas purity through regular checks and replacements if needed, this ensures optimal arc stability and weld penetration.
By following these guidelines, you can create a strong, permanent bond between cast iron and silicon bronze components while minimizing the risk of potential defects.