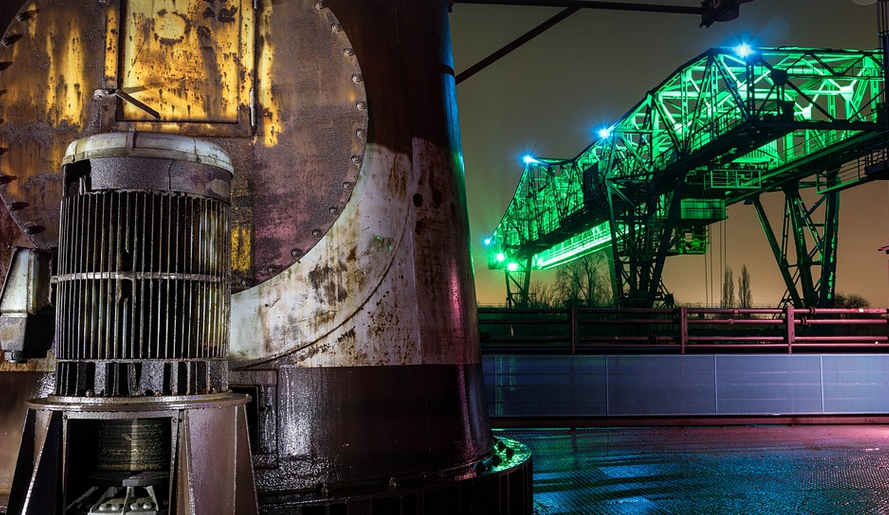
What’s MIG Welding, Anyway?
MIG welding, short for Metal Inert Gas welding, is a popular and versatile process that uses an electric current to melt metal, typically with shielding gas. Think of it like giving your project a little “weld-tender” kiss – the right kind of heat can join metals like butter and cream.
This process is often used for general construction projects, repairs, fabrication work, and even artistic endeavors (think welding art!). The beauty of MIG welding lies in its speed, ease of use, and relatively low cost compared to other welding methods.
Why Choosing the Right MIG Welding Wire Matters
We all want a smooth weld that’s strong enough to stand up to daily wear and tear. But picking the right MIG wire can make or break your project. Think of it like choosing the right paint – you wouldn’t use acrylic on wood, right? You need the right type of “weld-glue” for the job.
The best MIG welding wire depends heavily on what you’re building—steel, aluminum, stainless steel—and even which parts of your project will be exposed to various conditions.
Let’s dive into the world of MIG welding wire and discover what makes a good one!
Key Considerations When Choosing MIG Welding Wire
Choosing the right MIG welding wire is essential for achieving consistent, high-quality welds.
Here are some crucial factors to consider:
- Wire Diameter: The diameter of the wire determines how much metal it can carry. Thicker wires create stronger welds but increase travel speed and heat input. Thinner wires offer more weld control and accuracy, but may require more welding skill.
- Wire Composition: The composition of the wire dictates its properties. Some commonly used types include:
- **Steel Wires:** Solid steel wires are versatile, ideal for general fabrication and repair work due to their high strength and ability to weld various metals.
- **Aluminum Wires:** These wires are specifically designed for welding aluminum alloys, known for their lightweight properties. They provide excellent penetration and weld quality on aluminum.
- **Stainless Steel Wires:** Used for projects requiring high corrosion resistance. These wires create strong welds in stainless steel, offering superior durability.
Beyond the wire diameter and composition, other considerations include welding parameters (voltage, amperage) and your specific project requirements.
Why Understanding Welding Parameters is Crucial
Understanding the intricacies of welding parameters isn’t a bad thing! It’s an essential part of achieving high-quality welds.
Here’s why:
- **Voltage:** Affects the weld’s penetrating power, influencing how deeply the wire melts the base metal.
- **Amperage:** The current flow used to melt the metal at a specific point in the welding process.
- **Travel Speed:** How fast the welding gun moves along the joint. This directly affects the penetration depth and weld size.
Finding the right balance between voltage, amperage, and travel speed is crucial for creating strong welds and preventing spatter or inconsistent results.
The Importance of Welding Shielding Gas
In MIG welding, a shielding gas acts like a protective shield for your weld.
Think of it as the “safety” net that prevents contaminants in the air from interfering with the weld’s integrity. The right shielding gas ensures clean welds and helps prevent rust and corrosion.
Common choices include:
- **CO2 (Carbon Dioxide):** A cost-effective option commonly used for general steel welding, offering a consistent arc and good penetration.
- **Argon:** A popular choice due to its low cost and inert properties, allowing for clean welds on aluminum and high-temperature applications.
Choosing the right shielding gas depends largely on your project’s metal type and desired weld quality. Experimenting is part of learning!
Safety First: Always Prioritize Safety
MIG welding involves some heat, electricity, and fumes; so always prioritize safety!
Before starting any task, ensure you have the following:
- **Proper ventilation:** Keep your workspace well-ventilated to prevent harmful fumes from building up.
- **Eye protection:** Always wear welding goggles or a full face shield to protect your eyes and vision.
- **Fire suppression equipment:** Keep fire extinguishers readily available in case of an emergency.
Remember, safety is fundamental when working with electricity and high heat. It’s crucial to take the necessary precautions to prevent accidents and ensure smooth welding sessions!
Making the Right Choice: Choosing Your MIG Wire
Choosing the right MIG wire can make or break your welding project.
Here are some tips for finding the best one for you:
- **Project Type**: The first step is to determine what metal you’ll be working with. Steel, aluminum, and stainless steel each require a different type of wire.
- **Welding Parameters:** The welding parameters (like voltage and amperage) also play a critical role in choosing the right wire.
- **Manufacturer Reputation**: Research different brands to find those known for reliability and consistent quality.
By considering these factors, you’ll be on your way to finding the perfect MIG welding wire for all your projects!