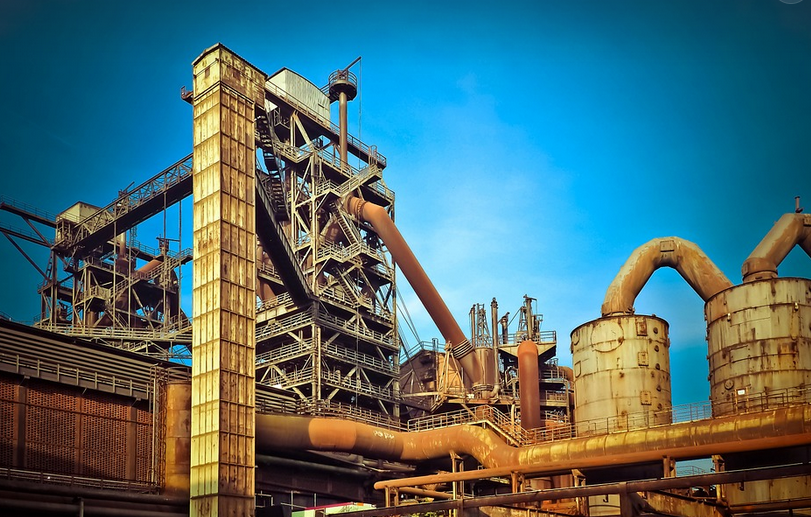
What is Spatter in Welding?
Welding, that magical fusion of metals, requires precision and control. Sometimes, however, things go awry, leaving behind unsightly spatter – little metallic specks that rain down on your work surface. These spatter particles are a common occurrence in welding processes like MIG, TIG, and SMAW (Shielded Metal Arc Welding). They’re not just an aesthetic eyesore; they can significantly hinder weld quality, creating porosity or weakening the joint.
Spatter is caused by several factors: molten metal droplets breaking apart when ejected from the electrode, arc instability, gas generation in the welding environment, and even the type of filler metal used. These factors lead to spattering that can be a major disruption to your welding process.
Why Anti-Spatter Spray is Essential
The good news is that combatting spatter isn’t about giving up on the welding process altogether. Enter anti-spatter spray, a potent solution designed to minimize and even eliminate these unwanted splatter particles. This specialized spray coats the welding surface, acting as a barrier against molten metal droplets.
Anti-spatter sprays work by various mechanisms:
- Surface Tension Reduction: The spray’s formula alters the surface tension of your weld puddle, reducing droplet formation and spattering.
- Water-Based Sprays: These sprays are easy to use and often very effective on various weld metals. They are readily available and usually cost-effective.
- Improved Weld Quality: Less spatter means a cleaner and more uniform weld bead.
- Increased Weld Speed: By eliminating the need to clean up spatter after each pass, you can increase your welding speed.
- Reduced Porosity and Cracking: Properly coated welds are less prone to porosity or cracking.
- Cleanliness is Key: Before applying the spray, ensure your welding area is clean of dust or debris. A clean surface allows for better penetration of the spray.
Application Tips for Anti-Spatter Spray
Applying anti-spatter spray requires precision and attention to detail:
- Thin Coats are Best: Apply a thin coat rather than a thick one to avoid clogging the weld joint and prevent uneven coverage.
- Dry Completely: Allow the anti-spatter spray to dry completely before welding. Waiting for it to fully cure ensures optimal protection against splatter.
Types of Anti-Spatter Spray
Choosing the right anti-spatter spray depends on several factors. You need to consider:
* **Type of Welding:** Different welding processes require specific sprays. For instance, TIG welding needs a different formula than MIG or SMAW welding. * **Weld Metal:** The type of filler metal used can dictate the best anti-spatter spray. Some sprays are specifically designed for certain metals like stainless steel.
There are several types of anti-spatter sprays available, each with its own distinct properties:
The Benefits of Using Anti-Spatter Spray
The advantages of using anti-spatter spray are numerous, making it a valuable tool for any welder:
Experiment with Different Solutions
The best way to find your perfect anti-spatter spray solution is through experimentation. Try different sprays from various brands and consult with experienced welders:
They can share their insights on what works best for specific welding applications.
Conclusion: A Welders’ Best Friend
Anti-spatter spray stands as a vital tool in the arsenal of any welder. This small investment pays off considerably, leading to better weld quality, increased efficiency, and reduced frustration. By incorporating anti-spatter spray into your welding routine, you can unlock a world of welding possibilities!