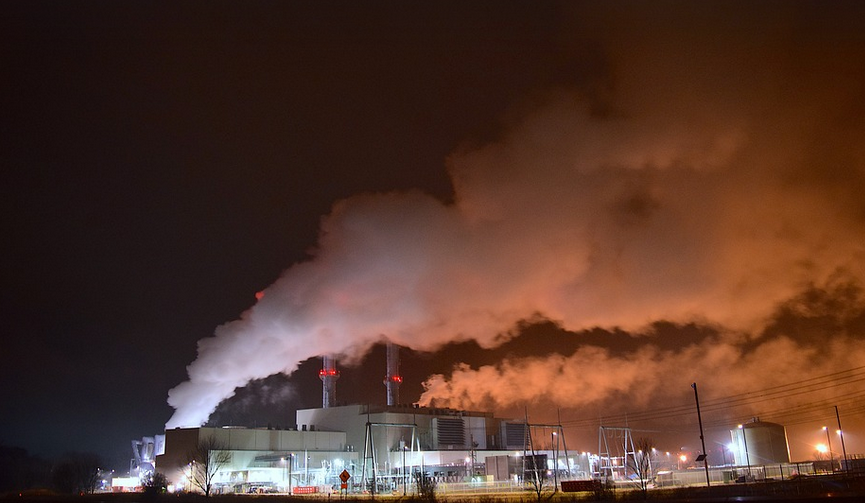
Understanding the Basics
CNC milling and routing are both crucial machining techniques used in various industries, from manufacturing to crafting. They share a common goal of creating precise shapes and patterns in materials using computer-controlled tools. However, each technique takes on unique approaches, leading to distinct advantages and disadvantages for specific projects.
CNC Milling: The Master of Precision
CNC milling uses rotating cutting tools with multiple axes of motion to precisely carve away material from a workpiece. It’s a versatile method that can create complex 3D shapes, intricate designs, and even perform delicate tasks like drilling or engraving. Imagine sculpting a statue – CNC milling is like having an incredibly precise sculptor’s tool for your work.
The process begins with creating a digital program, known as a G-code file, designed by a software specialist. This code controls the movement of the milling machine and directs its tools to follow pre-defined paths within the workpiece. The CNC milling machine then executes these instructions, utilizing various cutting tools like end mills or drills to precisely remove material.
CNC milling offers remarkable accuracy, repeatability, and speed. It’s an excellent choice when you need precise measurements and complex shapes. Its adaptability makes it suitable for a wide range of materials including metals, plastics, wood, and composites.
However, CNC milling isn’t always the most economical. Sometimes smaller-scale projects might not justify the high cost of specialized equipment and skilled operators, making other methods a better choice.
CNC Routing: The Artisan’s Approach
On the other hand, CNC routing relies on a different approach using a router with spinning cutters to carve specific shapes. Think of it like sanding down wood – the router carefully cuts away layers of material following pre-determined paths. This technique excels in tasks where precision matters but also requires intricate, even curves and contours.
Just like CNC milling, CNC routing starts with a digital design file. But unlike the precise movements of milling machines, the router’s approach is more focused on controlled cuts to achieve specific shapes. The router might work with wood, plastic, or foam; the choice depends on the project.
CNC routing offers unique benefits like creating curved and intricate designs, working with soft materials like foam for crafting, and even making decorative patterns in wood. It’s a good option for projects where a smooth finish is desired. Plus, it’s often cheaper than CNC milling due to simpler machinery.
However, CNC routing’s precision might not be as accurate as milling machines, especially when dealing with intricate detail or extremely thin layers of material. The ability to create complex shapes takes practice and skill that’s essential for achieving the final result.
Choosing Between Milling and Routing
Selecting the right machining technique depends heavily on your project’s specific requirements. Consider these factors to make an informed decision:
* **Shape Complexity:** For intricate designs or complex 3D geometries, CNC milling is often a better choice. * **Material Choice:** Milling can handle diverse materials like metals, plastics, and wood, offering versatility. Routing excels with softer materials like wood and foam based on the type of router used.
* **Budget:** Milling machines are more expensive than routers. However, this varies greatly depending on the machine’s features and capabilities. * **Skill Level and Expertise:** CNC milling requires specialized skills for both programming and operation, while routing can be easier to learn for beginners.
The Bottom Line
CNC milling and routing offer distinct advantages for their respective applications. Milling excels in precision and speed when dealing with complex shapes, while routing brings a unique artisan touch to softer materials. Carefully consider the specific requirements of your project before making a decision.