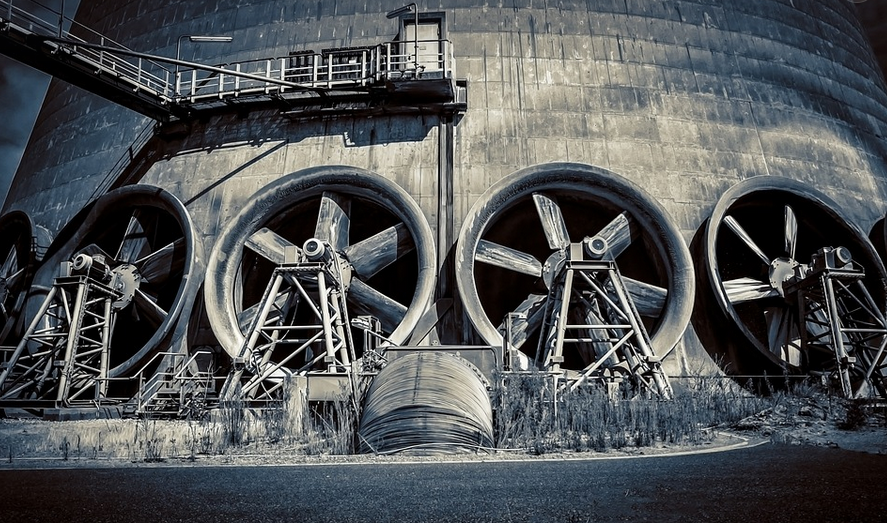
Unveiling the Lifespan of Your Welding Rods
You’re a welding enthusiast, passionate about bringing metal masterpieces to life. Whether you’re meticulously crafting automotive repairs or tackling intricate art projects, your welding rods are integral to your craft. But have you ever wondered if those seemingly eternal tools might succumb to the inevitable march of time? In this comprehensive guide, we delve into the fascinating world of welding rod lifespan and dispel the myths surrounding their deterioration.
Welding rods, unlike some other materials, don’t simply “go bad” in a traditional sense. Instead, their quality deteriorates over time, impacting their performance and longevity. This deterioration stems from several factors, including exposure to air, heat, moisture, and even the inherent chemical composition of the rod itself.
The lifespan of your welding rod varies significantly based on the manufacturer, material type, and storage conditions. High-quality rods, designed with optimal materials and careful manufacturing processes, can boast a longer shelf life than their cheaper counterparts. Think of it like this: you wouldn’t expect a fresh loaf of bread to last indefinitely in an open bag once left out for a week.
As welding rods age, they undergo subtle yet significant changes that affect their performance. The steel alloy within the rod can oxidize and form oxides. This process, known as galvanization, alters the surface area, potentially leading to increased spatter or a shorter weld bead life. You could say that over time, the once smooth surface of your rod becomes rough and uneven.
Moisture, particularly in humid environments, can wreak havoc on welding rods. Moisture promotes rust, which not only impacts the visual appeal but also hinders the overall performance of the rod. These rust-exposed areas are more prone to corrosion and can contribute to weakened connections.
Temperature, another critical factor, can accelerate deterioration. Exposure to extreme temperatures can lead to warping or even embrittlement in certain types of welding rods. Imagine holding a freshly baked loaf – it’s soft and pliable, but leave it out for too long, and it can harden like an old biscuit.
Storage conditions play a significant role in preserving the longevity of your welding rods. Proper storage ensures optimal shelf life by preventing exposure to harmful elements. Ideally, store your rods in a cool, dry, well-ventilated area. Avoid direct sunlight or strong winds that could affect the rod’s integrity.
Signs of deterioration are crucial for early detection and proactive measures. Inspecting for signs of discolouration, rust formation, or any physical changes can signal potential degradation. This visual inspection helps identify issues before they escalate to a major problem during welding operations.
While the question of “go bad” is more about deterioration than complete failure, it’s best to err on the side of caution. If you notice any signs of damage or degradation, consider replacing your welding rods for optimal performance and safety.