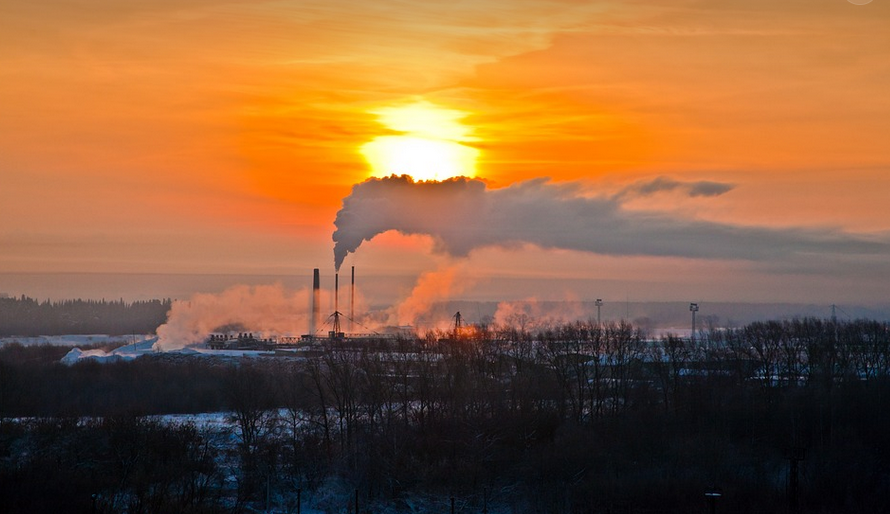
Understanding the Importance of Gas Coverage in TIG
So, you’re venturing into the world of TIG welding, and you’ve got your equipment ready to go. But before you start melting metal together, a crucial question pops up: what about argon? You see, TIG welding isn’t just about wielding the torch; it’s about understanding the intricate interplay between gas, heat, and metal.
Argon plays a starring role in TIG welding, acting as the silent guardian of your weld. Its job is to create a controlled atmosphere that minimizes oxidation – the unwelcome guest disrupting the beauty of a perfect weld.
Think of it this way: imagine trying to build a delicate mosaic on a dusty table. You need a clear space free from unnecessary particles. Argon’s role in TIG welding is much like this clean, protective environment for your weld pool. Without it, you risk creating unwanted oxidation, which can lead to weak welds and even dangerous flaws.
So, how much argon do you need? The answer isn’t a fixed number; it depends on several factors that impact the weld quality.
First, let’s talk about your TIG welding process. Are you using a pulsed TIG, which requires more control and finer adjustments to the current and travel speed, or a constant current TIG, which uses a more steady stream of energy? Understanding your specific welding technique is crucial for determining the correct amount of argon.
Next, consider your metal thickness. Thicker materials need a greater gas flow to ensure thorough shielding across the workpieces. It’s like giving a plant enough water to thrive; too little will stunt growth, and too much can overwhelm it. You want the right balance for optimal performance.
Also, remember that other factors, such as welding position and material type, might influence your argon usage. For instance, TIG welding on thin stainless steel requires a different approach than welding thick carbon steel, requiring adjustments to gas flow based on the specific requirements of each project.
Now, let’s delve into some real-world examples. One common rule is using 10 to 15% argon for every 90% shielding gas (the inert gas that prevents oxidation). But remember, this isn’t a hard and fast rule; the exact ratio should be tailored based on your specific situation. Experimentation and observation are always key during your welding process!
Another critical factor is your welder’s capacity to supply argon. A consistent argon flow ensures smooth welding operations without interruptions or inconsistencies in gas coverage. The ideal scenario is to have enough gas reserves to sustain the welding session without running into issues like interrupted welds.
Before you start, it’s crucial to ask your welding supplier about their recommendations for argon flow rate and shielding gas percentage. They’ll guide you towards the best practices based on your specific needs and welding environment.
Once you understand the factors that influence argon flow, you can easily adjust your settings. Using a TIG welder with an auto-gas control feature is an excellent way to achieve this. These features allow for automatic adjustments in gas flow based on the welding process parameters, eliminating manual intervention and reducing the likelihood of errors or inconsistencies.
Remember, precision is key when working with TIG welding and argon. The right amount ensures a clean, consistent weld pool without compromising the integrity of your project. By paying attention to these details and understanding the factors involved, you’ll be well on your way to mastering the art of TIG welding.
If you’re ever unsure about how much argon to use or what settings to choose for your TIG welder, don’t hesitate to reach out to a qualified welding instructor for help. They can provide valuable guidance and expert insights specific to your project and welding technique.
Happy welding!