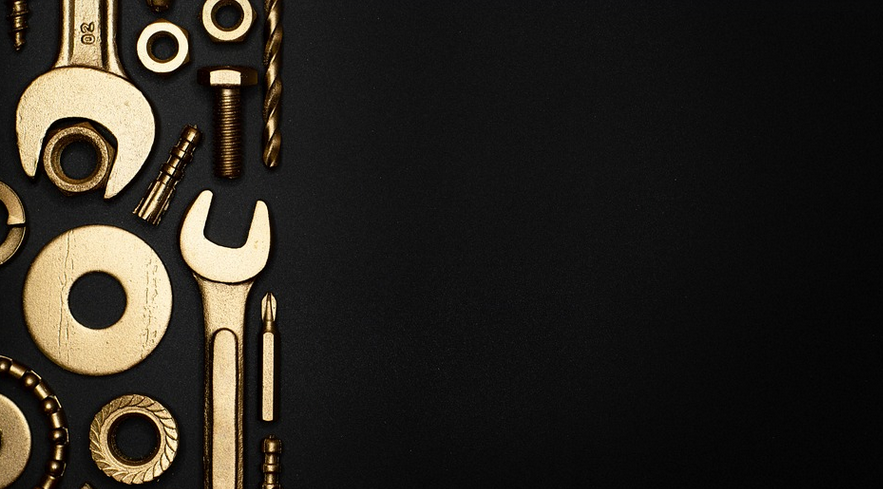
Say Goodbye to Burnout
Let’s face it, soldering can be a bit of a pain. You’ve got your heated iron in hand, waiting for the solder to flow and join your wires together – but sometimes things just don’t go according to plan. Whether you’re battling high temperatures or dealing with stubborn joints, there’s a good chance you’re looking for that “easy-peasy” soldering experience. Well, enter the game-changer: induction heating soldering irons.
What Makes Induction Heating So Special?
Induction heating soldering irons are taking the world by storm. They use electromagnetic induction to heat the workpiece directly, eliminating the need for a traditional resistive iron tip. This means no more scorching your components or burning materials – just pure, efficient melting action.
How does it work exactly? It all starts with a coil within the soldering iron that creates a magnetic field. When this magnetic field interacts with the conductive workpiece (like a metal sheet or a component), electrons are excited, ultimately generating heat. This technology is like magic – but for soldering!
Benefits Beyond Just Efficiency
But the benefits go way beyond just speed and temperature control. Induction heating offers a host of advantages that traditional soldering irons can’t match:
- Precision Control: The ability to heat elements precisely allows for fine-tuning, ensuring accurate solder application and avoiding potential overheating.
- Reduced Heat Loss: No more heat transfer to the environment! Induction heating minimizes heat loss thanks to its highly efficient process. This translates into lower energy consumption and a more comfortable soldering experience.
- Cleanliness Advantage: Say goodbye to messy solder dripping. The absence of traditional contact between the iron tip and the workpiece reduces chances of smoldering, leading to cleaner workspaces and less frustration.
Practical Applications – From Electronics to Automotive
Induction heating soldering irons have a diverse range of applications across various industries. Let’s explore some key examples:
- Electronics: From intricate microchip assembly to complex circuit board repair, induction heating allows for high-precision work on delicate components, ensuring efficient solder joints and minimal damage.
- Automotive Industry: Induction soldering is widely used in the automotive industry. Whether it’s welding wires or connecting electronic components in a car chassis, this technology ensures fast, clean, and durable connections.
- Robotics and Automation: The ability to heat workpieces precisely with minimal energy consumption makes induction heating ideal for robotic applications where precision is paramount. It allows for automated soldering tasks across various industries.
Choosing the Right Induction Soldering Iron
Now that you’re excited about the possibilities, let’s talk about choosing the right induction soldering iron. There are different types on the market based on power and features:
- Power output: Consider your specific project requirements. The power output determines the workpieces it can handle effectively. For high-power applications, a higher wattage is needed.
- Frequency: Soldering frequency affects the speed and precision of heating. Different frequencies cater to different materials and soldering tasks.
- Ergonomics & Design: Opt for an induction soldering iron with a comfortable grip, intuitive controls, and a durable design that can stand up to regular use.
The Future of Soldering is Here
Induction heating soldering irons are revolutionizing the way we solder. The benefits are undeniable, encompassing increased precision, efficiency, and cleanliness. As technology continues to advance, expect even more innovative applications in various fields. So, go ahead – embrace the future of soldering with an induction heating soldering iron!