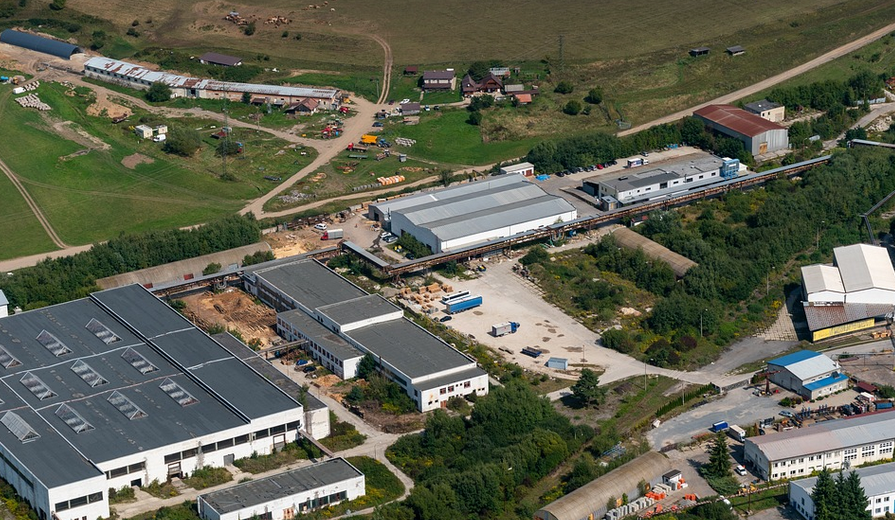
Unlocking Precision in Your Welding Shop
There’s a certain charm and functionality to a well-set up jig table – a welding shop staple that often gets overlooked amidst the whirring of welders and the clang of metal. These tables, though seemingly ordinary objects, serve as the backbone of precision work in any welding environment.
What Makes a Jig Table So Special?
Unlike your average workbench, jig tables are built for one thing: to hold and manipulate precise workpiece configurations. Their sturdy construction, often featuring high-quality steel or aluminum beams with carefully engineered cross bracing, guarantees an unwavering platform capable of holding heavy components.
Jig tables boast a unique set of features that differentiate them from conventional work surfaces. First, they are designed to provide maximum stability and support for even the most demanding welding projects. Their sturdy construction allows them to withstand the weight of multiple pieces and tools, ensuring the integrity of your work.
Secondly, many jig tables come equipped with a range of features that amplify their versatility. Integrated vise or clamping systems provide secure positioning for parts during welding operations, while additional slots and holes allow for the attachment of specialized accessories like angle clamps, support beams, and even lighting fixtures.
The Welders’ Secret Weapon
Jig tables aren’t just tools for holding metal; they are crucial components in the success of any welding project. Their ability to hold parts accurately ensures consistent welds, minimizing errors and improving overall efficiency.
Think about it: when you weld a part on a jig table, you create a stable environment where precision is paramount. The table acts as a foundation, ensuring everything remains in alignment during the welding process. This meticulous control translates to high-quality welds that are visually appealing and functionally sound.
Jig tables often enable multiple tasks within the same workspace, which simplifies the workflow and boosts productivity. For instance, they can serve as a dedicated platform for pre-weld preparation, such as aligning components, drilling holes, or applying welding masks. This allows welders to stay organized and focused on achieving optimal results.
Types of Jig Tables
The world of jig tables is incredibly diverse, with specialized models catering to specific needs. One popular type is the “welding fixture” table; these are designed for high-volume welding projects and feature long worktables with sturdy mounting points for various tools.
Another common type is the “jig table” designed for intricate welding tasks, such as joining custom shapes or components. These tables often come equipped with a variety of clamps and tools for precise metalworking operations.
Jig Table Advantages: A Breakdown
The benefits of using jig tables in your workshop are numerous. Here’s a closer look at some key advantages:
- **Improved Weld Quality:** Precise alignment and controlled positioning ensure consistent, high-quality welds.
- **Enhanced Productivity:** Dedicated workspaces enable streamlined workflows, minimizing downtime and maximizing efficiency.
- **Reduced Error Rates:** The precision of jig tables minimizes human error, leading to accurate and reliable welds.
- **Safety First:** The secure holding system ensures stability and prevents objects from falling during the welding process.
- **Versatility:** Many table models support multiple tasks like pre-weld preparation and assembly, streamlining workflow.
Your Welding Shop’s Blueprint for Success
Investing in a quality jig table can be an investment that pays dividends. Not only does it streamline your welding process but also reduces errors and improves overall weld quality. The increased efficiency translates into quicker turnaround times, saving you valuable time and resources.
Furthermore, using a jig table demonstrates a commitment to precision welding, which can be vital for specific industries such as automotive and aerospace, where precise welds are paramount. This dedication shows professionalism and builds your reputation in the industry.