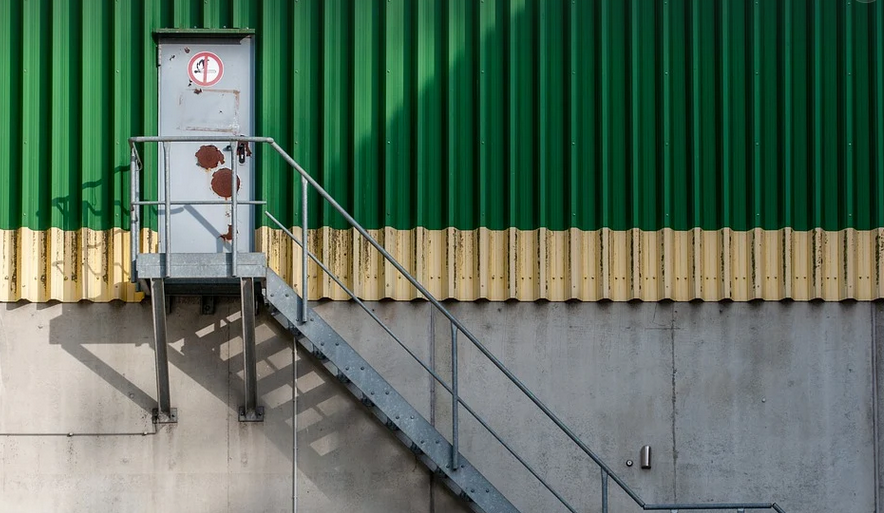
The Ultimate Guide to Metal Joining Methods
Have you ever wondered about the magic behind creating strong, lasting welds using electric currents? Well, it all boils down to two main players in the metal welding arena: MAG welding and MIG welding. Both offer a fantastic way to join metals for various projects, from home repairs to industrial applications.
Both techniques utilize similar principles of transferring heat and melting metals together. Yet, they differ subtly in their approaches, leading to variations in speed, efficiency, and the final weld quality you achieve. Choosing the right technique depends on factors like your welding needs, experience level, budget, and desired outcome.
Understanding the Fundamentals: What’s MAG Welding?
MAG welding stands for **Metal Arc Gouging**. This method utilizes a shielded metal arc (SMA) for joining ferrous metals. Imagine a high-powered electric current flowing through an electrode that melts the base metal, effectively joining them together. A coating of flux-covered wire is then used to create a protective shield around the weld pool and prevent oxidation.
MAG welding offers numerous advantages thanks to its robust technology: higher welding speeds, enhanced penetration (depth), smoother welds with less splatter, and excellent arc stability and control. But it’s not just about speed; the technique also excels at creating highly precise welds on a variety of materials.
The benefits of using MAG welding can be summarized as follows: increased weld quality, reduced slag formation, improved weld penetration, better control over weld bead shapes, and enhanced corrosion resistance. However, it’s not without its challenges; the equipment required is expensive, making it a less popular choice for hobbyists compared to MIG welding.
The MIG Welding Advantage: Simplicity and Versatility
MIG welding stands for **Metal Inert Gas** welding, a technique that uses a continuously fed wire electrode coated in flux to create a weld. You can think of the process as an electric current melted through the wire, creating a molten puddle on the base metal.
MIG welding is known for its simplicity and versatility. It relies on readily available equipment, making it a popular choice for beginners starting their welding journey. The streamlined process allows for faster welding speeds, especially with automated systems, contributing to increased efficiency and productivity.
The key advantages of MIG welding include: affordability, ease of use, high-speed production rates, versatility in material selection (including stainless steel), and a relatively low learning curve compared to other methods like TIG welding. Though it comes with some limitations, such as potential splatter and lower penetration levels on thicker materials.
Choosing Your Weapon: Which Technique Suits You?
As you explore the world of welding, comparing MAG and MIG is crucial for making informed decisions. Consider these factors to determine which technique aligns best with your needs:
- Project Type : Are you tackling repairs on a small appliance or manufacturing large industrial components?
- Weld Quality Demands: Do you require precision welds for critical functions like automotive parts or delicate electrical wiring?
- Skill Level and Experience: Are you new to welding, or are you confident in your abilities?
- Budget Considerations: How much can you invest in welding equipment based on the type of projects you plan to tackle?
Going Deeper: Exploring the Differences
Let’s delve a little deeper into some specific comparisons to understand the nuances between these methods:
Welding Speed and Productivity: MIG welding generally offers faster speeds, making it ideal for high-volume applications or projects requiring quick production times. On the other hand, MAG welding might deliver slightly slower speeds due to the intricate process involved with shielding gas management.
Weld Penetration and Control: Both techniques facilitate penetration through metals, but MIG welding traditionally excels in controlled bead formations and precise weld control. However, its use of flux-core wire can sometimes lead to splatter, while MAG welding offers better arc stability and control over the weld pool.
Material Compatibility and Weld Quality: Both techniques are versatile, handling various metals. However, MAG welding is preferred for applications requiring high-quality welds on ferrous metals due to its consistent bead formation and superior penetration capabilities. Conversely, MIG welding is suitable for a broader range of materials, including stainless steel, offering excellent weld quality in many situations.
Safety Considerations: Both techniques require safety precautions like proper ventilation, personal protective equipment (PPE), and training to avoid accidents. However, MAG welding typically involves higher levels of risk due to the use of shielding gases, emphasizing the importance of expert guidance for safe operation.
The Verdict: MAG vs MIG – The Choice is Yours!
Ultimately, choosing between MAG and MIG depends on your individual needs and circumstances. Whether you prioritize speed and ease of use with MIG welding or seek greater precision with MAG, both techniques offer valuable solutions in the world of metalworking. Don’t hesitate to seek expert advice from experienced welders if you are unsure.
Embracing Welding: A Welcoming Journey
The art of welding is a fascinating skill that opens doors for countless possibilities. Whether you’re embarking on home repairs or pursuing career opportunities, understanding the nuances between different welding techniques will empower you to make informed choices and create lasting, beautiful results.