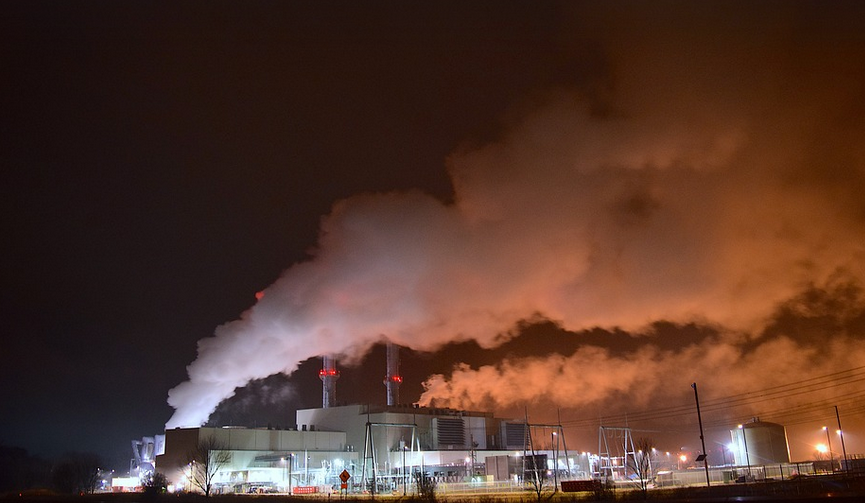
The Power of Precision: What is Metal Cored Welding Wire?
Imagine this: you’re working on a project, be it welding a metal bridge, repairing a rusty car, or even just modifying your living room furniture. You need something that can withstand high temperatures and pressures while delivering a strong hold. Enter metal cored welding wire – the unsung hero of countless industries.
What makes this unique is its composition: it’s basically a core of solid metal surrounded by a flux-coated layer of filler material. This allows for precise control over weld penetration, bead shapes, and ultimately, the final product’s strength and smoothness. Unlike traditional welding methods that rely on bulky electrodes or even molten metals, Metal Cored Welding Wire offers a cleaner, faster, and more reliable option.
The Advantages of This Mighty Weld: A Closer Look
Metal cored welding wire isn’t just a fancy name; it’s built for real-world applications. Let’s explore some key benefits:
* **Exceptional Heat Transfer:** The core acts as a thermal conductor, allowing the filler material to flow and solidify at optimal temperatures for efficient welding and reduced heat distortion.
**Increased Seam Strength:** The wire’s structure enhances weld penetration and fill-ability, leading to stronger welds that can withstand stress and weather conditions.
* **Enhanced Welding Speed:** With its ability to conduct heat efficiently, it reduces the time needed for welding processes, making projects faster and more efficient.
**Reduced Spatter and Slag:** The flux coating on the wire minimizes spatter production, leading to cleaner welds with less cleanup effort.
Understanding the Anatomy of a Metal Cored Wire
To truly appreciate the power of metal cored welding wire, you need to understand how it works. Let’s delve into the heart and soul of this incredible technology:
* **The Core:** This is typically made from steel or other alloys like nickel or cobalt. Its strength and resilience are essential for handling high temperatures during welding.
**The Flux Coating:** A crucial component, this layer protects the core and ensures an even melt flow. It also helps to keep the weld clean by removing slag and debris.
**The Diameter:** The wire diameter is a critical factor in determining how much metal it can transfer during welding. Smaller diameters are better for thin metals, while larger ones handle thicker material.
Finding the Right Wire: Matching Your Project to the Solution
Choosing the right metal cored welding wire depends on your specific job. Here’s a quick guide to help you select the perfect match:
* **Material Type:** The base metal being welded (steel, aluminum, etc.) should be considered. Different wires have unique alloys that make them ideal for specific materials.
**Weld Position and Welding Style: ** Whether your welding is done in a horizontal position or requires submerged arc welding, choose a wire designed for the specific task.
**Welding Current and Voltage:** The amount of electric current used to initiate the weld will affect the speed and efficiency of welding.
Metal Cored Welding Wire: A Look at the Future
Metal cored welding wire is a powerful tool that continues to evolve and improve. Here’s a glimpse into what the future holds:
* **Increased Precision Control:** The development of increasingly accurate welding parameters allows for even finer control over weld quality, offering more precision than ever before.
* **Hybrid Applications:** Combining metal cored wire with other advanced techniques promises innovative solutions in industries like aerospace and automotive engineering.
The future of welding is bright, fueled by the advancement of materials and technology. Metal cored welding wire stands as a prime example of this progress, offering a faster, cleaner, and more efficient way to weld.