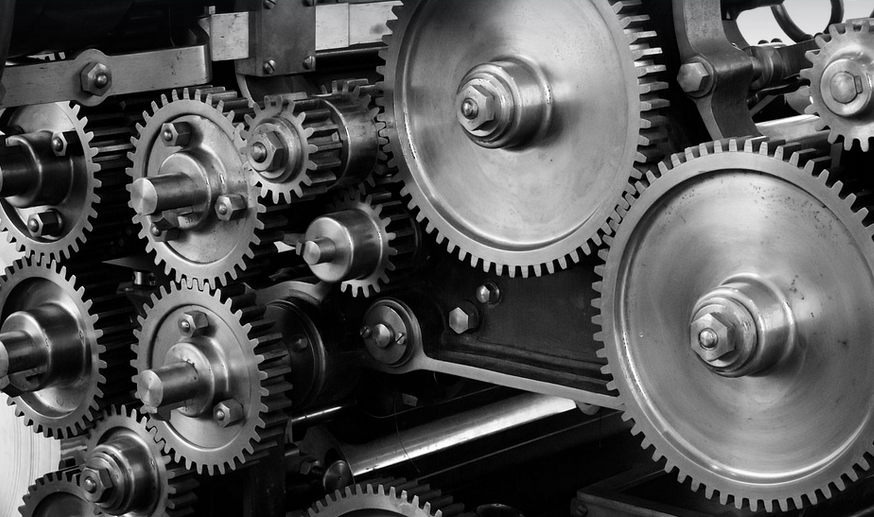
What is Chrome Moly Steel?
Chrome molybdenum steel, often abbreviated as CrMo or just “chrome moly,” is a popular type of stainless steel known for its incredible strength and high-temperature resistance. This versatile material finds applications in everything from automobiles to airplanes and even everyday construction projects. But why does it matter when welding with mig?
The unique blend of chromium and molybdenum adds a significant amount of tensile strength, making chrome moly steel significantly more robust than traditional steel. However, this very property – its high tensile strength – can pose some challenges for welders.
Understanding the Challenges
One major challenge with welding chrome moly is the material’s tendency to bridge under heat from the welding process. This leads to “porosity” – tiny holes that create weak spots in the weld and ultimately weaken the overall structure of your project.
Additionally, chrome moly can be a bit more sensitive to the welding electrode’s type. While there are many good options available for this material, some may produce a higher level of porosity than others.
Choosing the Right Electrode
The right electrode is crucial when tackling chrome moly. It needs to be designed specifically for high-strength materials like this and offer excellent penetration while minimizing porosity. A common choice is a 0.035″ or 0.045″ diameter welding electrode, usually made from tungsten.
Another important factor in choosing the right electrode is understanding its shielding gas requirements – it’s crucial for preventing oxidation and ensuring a smooth weld.
Mig Welding: A Step-by-Step Guide
When using mig welding for chrome moly, you need to follow a few essential steps. These will help you achieve consistent, high-quality welds.
- Prepping the Metal: It’s important to clean and prep your metal before you start welding. Remove any rust or debris from the surface. Also, consider using a grinding wheel for smoothing out rough spots.
- Pre-weld Cleaning: Before applying the electrode, ensure that it’s free of dust.
- Setting Up the Welding Machine: Make sure your welding machine is set to the correct amperage for the thickness of your chrome moly. You’ll also need to select the appropriate wire feed speed and welding voltage based on the material you are welding and the type of weld you’re making.
- Apply the Electrode: With a steady hand, apply the electrode to the metal. Use a consistent touch force for even heat distribution across the surface.
- Welding Process: Start by welding slowly and in small sections to ensure good control and penetration. Apply gentle pressure on the electrode as you move along the joint.
- Weld Finishing: After completing your weld, finish it with a grinding wheel or file for a smooth look.
Avoiding Common Mistakes
1. Welding Too Fast
Welding too fast can lead to improper penetration and uneven heat distribution, potentially causing porosity and weak welds.
2. Not Using the Right Electrode
Choosing a welding electrode that’s not designed for chrome moly can impact weld quality. Always use a dedicated electrode for this material.
3. Not Prepping the Metal Properly
Cleaning and prepping your metal before welding is crucial, as dirt and rust can create weak points and reduce weld quality.
Mastering the Art of Mig Welding Chrome Moly
With a little practice and the right understanding of techniques, you’ll master mig welding chrome moly. Remember that patience is key when it comes to this material – take your time and focus on building solid welds with perfect penetration.
By following these steps, you can increase the success of your projects and enjoy the benefits of working with high-strength materials like chrome moly steel.