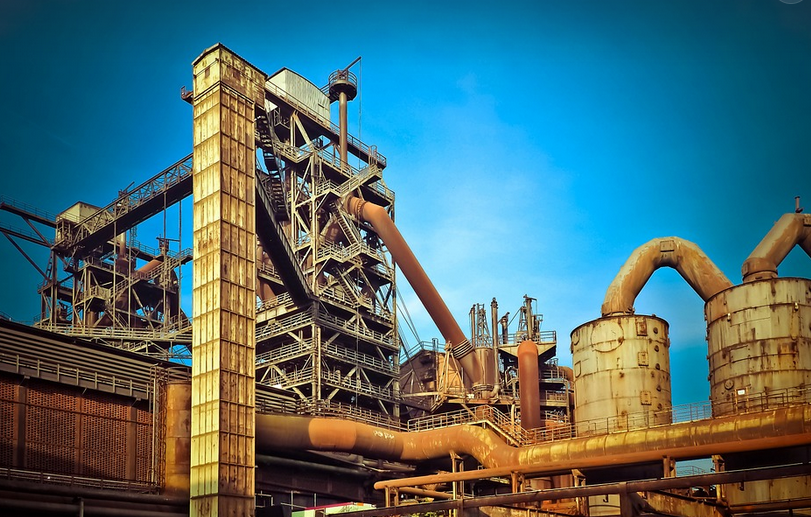
Not Just for Protection: Understanding the Importance of Nose Plugs
Welding, a craft steeped in tradition and precision, provides some truly awe-inspiring feats of metal manipulation. But beneath the artistry lies a realm where heat and fumes reign supreme, demanding our utmost attention and protection from unseen hazards. And that’s where nose plugs come in.
Imagine welding as an intense dance between fire and metal – a symphony of sparks, flames, and molten pools. It’s no wonder that the scent of burning steel permeates the air, a sharp reminder of the raw power of the forge. But this potent blend of fumes isn’t just unpleasant; it can be significantly dangerous to our health.
Fumes are not only an irritant but also potentially toxic, containing hazardous chemicals like hydrogen sulfide (H2S), which can cause serious respiratory problems, even fatal in extreme cases. Welding fumes can linger long after the flames die down, clinging to your clothes and equipment for a long time.
Nose plugs, those seemingly simple devices that add a layer of protection to daily life, take on an entirely new meaning when it comes to welding. Wearing them isn’t about just preventing odor; it’s about safeguarding our respiratory well-being in the heart of the welding arc.
Think of your nose as one of the first lines of defense against this potent mix of fumes. The delicate nasal cavity, designed to filter and warm air before it reaches the lungs, is a prime target for these harmful airborne particles. Nose plugs act as shields, ensuring that these microscopic invaders are diverted away from our crucial respiratory system.
But nose plugs aren’t just about preventing inhalation; they also play a role in enhancing overall welding performance and comfort.
For welders who spend long hours hunched over their work, nose plugs can provide much-needed relief from the constant sting of fumes and heat. This can drastically improve focus and concentration, allowing for greater precision and productivity.
Imagine a welder working on a critical structural steel beam; if they are battling against the onslaught of welding fumes, it’s like trying to paint the Mona Lisa with your eyes closed. The result? Subpar work quality and wasted time.
Nose plugs offer a lifeline in this arena, creating a safe haven for their breathing while they shape metal into masterpieces.
By wearing nose plugs, welders can enhance their concentration and focus on the task at hand.
Types of Nose Plugs for Welders: Choosing the Right Fit
The world of nose plugs is diverse, with various styles designed to cater to the specific needs and preferences of each welder. Let’s delve into some common types:
**Silicone Plugs:** These are the most popular choices, known for their flexibility and comfort.
Advantages:
* Comfortable fit: Their soft silicone material conforms to different nose shapes without causing pressure.
* Easy to use: They’re simple to insert and remove.
**Foam Plugs:** Another popular option, known for its exceptional noise reduction ability. These plugs come in various densities and thicknesses.
Advantages:
* Effective against fumes and wind noise: They provide a substantial barrier against harmful particles. They also offer protection against loud noises during welding.
* Customizable fit: Foam plugs can be molded to different nose shapes for optimal comfort.
**Gel Plugs:** These are often preferred by welders working in high-pressure environments where rapid heat and harsh fumes are encountered.
Advantages:
* High impact resistance: Gel plugs can withstand the sudden shifts in pressure while welding.
* Easy to maintain: They’re relatively easy to clean and replace.
The right choice depends on a welder’s specific needs. Some prefer the gentle embrace of silicone, while others crave the firm grip of foam or gel.
But remember, choosing the best nose plugs isn’t just about comfort; it’s about ensuring maximum protection during welding.
Navigating Welding Fumes: An Essential Safety Guide
Welding fumes are not just a nuisance but can significantly impact our health and well-being.
Here’s a quick rundown of the most common types of welding fume, their associated hazards, and preventative measures:
**Hydrogen Sulfide (H2S):**
This colorless gas with a distinct rotten egg odor is a potent respiratory irritant that can cause severe health problems. It’s found in welding fumes emanating from various metals like iron, sulfur, and nickel.
**Carbon Monoxide (CO):** The colorless and odorless CO produced during combustion is another hazardous component of welding fume. It displaces oxygen in the body, leading to dizziness, confusion, and even death if not addressed quickly.
**Other Fume Types:**
Welding fumes also contain particulate matter such as lead and copper. These can cause respiratory problems like lung irritation, coughing, and shortness of breath.
**Preventing the Impact:**
Here are some essential strategies for mitigating fume exposure during welding:
* **Proper Ventilation:** Make sure your welding area has adequate ventilation to clear out fumes. Use fans or exhaust systems to remove harmful particles from the air.
* **Protective Gear:** Equip yourself with a full-face respirator equipped with an appropriate filter to prevent inhalation of harmful particles.
* **Regular Maintenance:** Carefully inspect welding equipment regularly for any potential leaks or damage that might exacerbate fume exposure.
A Final Word: Prioritizing Health and Safety in the Welding Arena
Welding, in its majestic complexity, requires a deep understanding of both its intricacies and safety measures. Nose plugs are not just an optional accessory; they embody this commitment to well-being.
By embracing these simple tools, welders can safeguard their health, heighten performance, and dive deeper into the realm of metalwork with confidence.
In the end, protecting our respiratory system is a vital part of responsible welding – ensuring a safe and productive work environment for everyone involved in this intricate art form.
So go forth, welder. Embrace the heat, but never forget to prioritize your health!