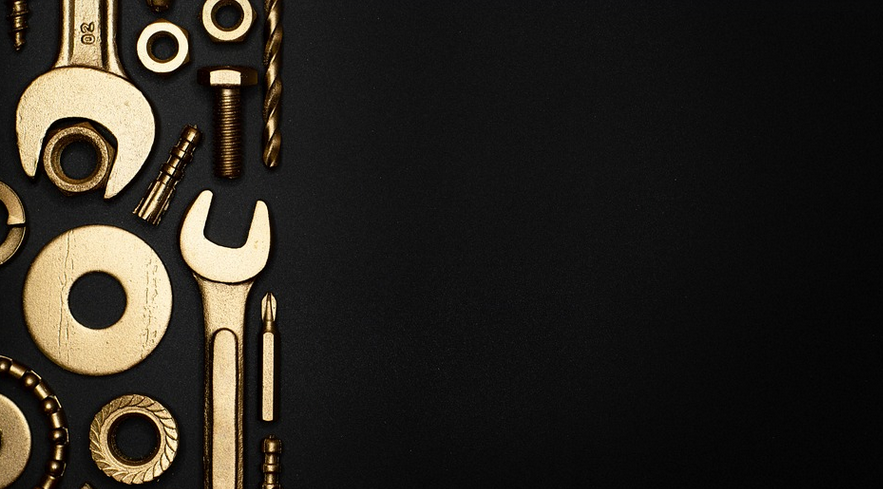
What Makes a Project Special?
In the world of industrial manufacturing, “specialty welding” might sound like a fancy name for just another type of welding. But trust us, it’s so much more than that! This involves tackling projects with unique challenges – whether it’s working on delicate components in medical devices or fabricating massive structures for power plants. It’s about precision and expertise.
Imagine needing to join two pieces of steel together under immense pressure while maintaining specific tolerances. That’s where specialty welding shines! It requires a deep understanding of the materials, processes, and safety protocols needed to ensure quality without compromising on speed or efficiency.
The Power of Turnaround
Now, imagine having your project completed faster than ever before. This isn’t just a dream; it’s the power of “turnaround” welding. It’s about maximizing output and minimizing downtime in a way that traditional welding often struggles to achieve.
Turnaround welding is all about speed, precision, and efficiency – three pillars on which any successful project relies. It utilizes specialized techniques, equipment, and skilled labor to complete complex welds with minimal disruption to the overall production schedule. Think of it like this: instead of waiting for a welder to finish their work before moving onto the next job, turnaround welding allows you to continuously build and progress!
Why Choose Specialty Welding?
So why choose specialty welding for your project, rather than just sticking with regular welding techniques?
Let’s delve into a few key reasons:
- Precision & Accuracy: Specialty welders are trained to work with delicate materials and intricate designs. This translates to superior weld quality, reducing the need for costly rework and ensuring longevity.
- Customized Solutions: From medical equipment to aerospace components, specialty welding offers a level of customization that traditional welding simply can’t match. This ensures your project meets specific needs and functionality requirements.
- Safety & Expertise: The safety of personnel and the integrity of the final product are paramount in specialty welding. Certified welders understand the intricacies of various materials, ensuring safe handling and efficient fabrication.
- Time-Saving Efficiency: By leveraging specialized techniques, turnaround welding streamlines workflows, allowing for faster completion times and minimizing downtime. This translates to greater productivity for your project.
And there’s so much more! From robotic welding and high-voltage applications to underwater welding and complex pipe fabrication, the world of specialty welding offers endless possibilities.
Turnaround: The Efficiency Engine
Turnaround welding is not just about speed; it’s a strategic approach that considers efficiency in its entirety. It revolves around meticulous planning, streamlined workflows, and well-trained personnel. It’s a whole new level of operational excellence.
Here’s how turnaround turns the manufacturing experience into a smooth ride:
- Pre-Planning: A deep understanding of your project needs ensures efficient resource allocation and minimizes delays.
- Optimized Scheduling: By working with dedicated teams, clear communication channels are established, and schedules are optimized to minimize wasted time.
- Dedicated Equipment: High-quality equipment is essential for efficient turnaround welding. It’s the backbone of speed, precision, and accuracy.
- Skilled Professionals: Specialty welding requires a team of highly skilled welders who understand the nuances of each project, from intricate designs to complex materials.
The Future of Specialty Welding
As technology advances, so will the future of specialty welding. We’ve seen robots taking over repetitive tasks and AI driving precision in welding applications. This means even more opportunities for efficiency and accuracy in the years to come.
Here are a few trends shaping the landscape:
- Advanced Robotics: Robotic arms and automated systems become increasingly sophisticated, leading to faster welding speeds and greater precision.
- Artificial Intelligence: AI-powered software is being used for weld quality control and predictive maintenance, ensuring accuracy and minimizing downtime.
- 3D Printing: Additive manufacturing will continue to play a crucial role in designing complex components and reducing the need for traditional welding techniques.
- Sustainable Welding Practices: Companies are exploring eco-friendly welding methods, resulting in greater efficiency while minimizing environmental impact.
Ready to See the Difference?
If you’re looking to elevate your manufacturing process and maximize efficiency, specialty welding is an obvious choice. It’s about exceeding expectations, from intricate designs to robust structures. It’s about creating a seamless experience from project conception to completion.