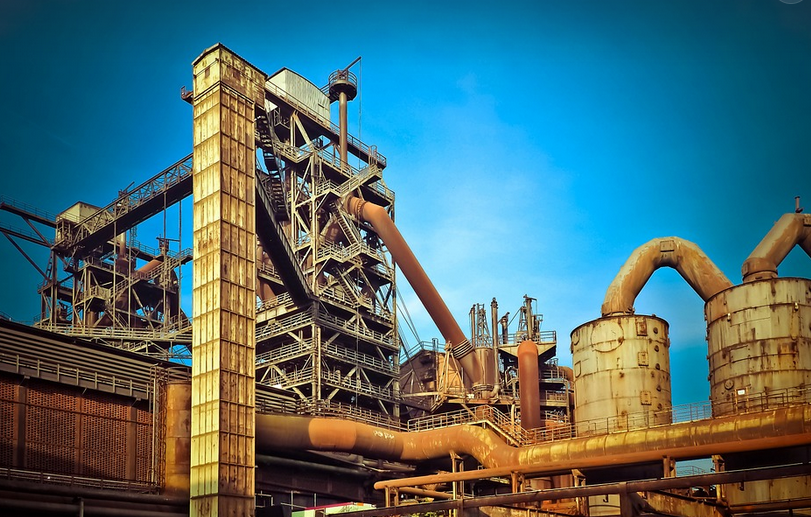
Understanding the Basics
When it comes to welding, precision and reliability are paramount. Choosing the right welding rod is a crucial step towards ensuring quality welds and lasting results. One of the most commonly used welding rods in the industry is 6011. It’s known for its versatility, forgiving nature, and ability to deliver effective welds on various materials, making it a staple in workshops and fabrication shops alike.
What Makes 6011 So Special?
The magic of 6011 lies in its unique combination of properties. It is a low-hydrogen electrode welding rod designed for use with shielded metal arc welding (SMAW), also known as stick welding. The “6” and “11” refer to the welding rod’s composition, specifically its nickel content. This translates to a high amount of ferros (iron) in the rod itself, leading to excellent penetration and strength in welds.
The 6011 is designed for use with AC or DC power sources. It offers a good balance between welding speed and weld quality, making it suitable for both indoor and outdoor applications.
Powering Up: Amperage Control
One of the key factors influencing the effectiveness of 6011 welding is the amp setting on your welder. You might be wondering what the significance of 3/32 amps is. Here’s why it’s important. It all comes down to the amperage, or the amount of electrical current flowing through the welding rod.
When choosing the right amperage for 6011, you need to consider several factors. First and foremost, the type of metal you’re working with plays a crucial role. Thinner materials like sheet metal might demand lower amperage settings, while thicker steel plates could benefit from higher amperage.
Think about it this way: A higher amperage setting can result in faster welding speed and deeper penetration, but it also increases the heat input into the joint, potentially leading to warping or distortion. It’s essential to find a balance between speed and precision.
Understanding Amperage and Arc Characteristics
The 3/32 amp setting on your welder is where you’ll find the sweet spot for welding with 6011 rods. It strikes a balance between achieving good weld penetration, weld bead quality, and minimizing potential distortion.
Here’s why this amperage range works so well: It allows for smooth arc travel and consistent heat input to the joint. The lower current flow helps control spatter and improves weld puddle fluidity.
The Importance of Proper Technique
While selecting the right amperage is important, remember that getting great welds comes down to proper technique as well. Welding requires skill and precision. You need to focus on: * **Maintaining a consistent arc length:** This ensures even heat distribution across the weld joint. * **Controlling the welding speed:** A controlled pace helps you achieve smooth arcs and minimize distortion.
Choosing Your 6011 Rod
There are several variations in 6011 rods, which can affect their properties and performance. Key factors to consider when selecting your rod include: * **Welding position:** Whether you’re working on flat surfaces, overhead, or vertical positions will influence the welding process. * **Material thickness:** The thickness of the metal being welded determines the type of electrode rod you need. * **Weld joint design**: The shape and size of your weld joint also play a role in choosing the correct rod.
6011: A Durable Weld for a Lifetime
One of the significant advantages of 6011 welding rods is their durability, which makes them suitable for applications that require long-lasting welds. The high nickel content allows for excellent strength and resistance to corrosion. This ensures your welds will be able to withstand wear and tear over time.
When it comes to choosing the right welding rod, don’t settle for anything less than quality. 6011 offers a reliable combination of performance, affordability, and ease of use, making it a valuable tool in any welder’s arsenal.