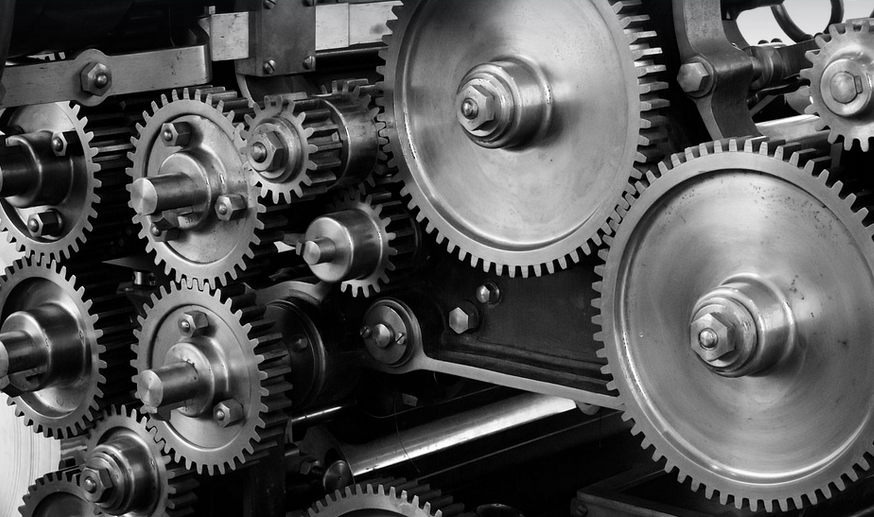
What’s the Big Deal About Rod Diameter?
Let’s talk about tig welding rods. You might have heard this term thrown around a lot, especially if you’re venturing into the world of metal fabrication and repair. But what exactly is a “tig welding rod” and why does its diameter matter so much?
At its core, a tig welding rod is nothing more than a solid wire designed to generate heat during the welding process when subjected to an electric arc. Think of it as your personal metal-welding chef’s knife—it’s sharp, precisely crafted, and ready to melt those metals together.
These rods come in various diameters, and this is where the real fun begins, especially for experienced welders. The diameter acts like a gauge for how much current and heat the welding rod will deliver. A bigger diameter generally means more power and heavier deposits, while a thinner one means less current, leading to finer control and precision.
But understanding the link between rod diameter and weld quality goes beyond just power levels. It’s a crucial factor in achieving those coveted “smooth,” “clean,” and “consistent” welds that are so desirable in any welding scenario.
Understanding Rod Diameter Basics
Let’s delve into the details of how rod diameter affects your tig welding process:
**Rod Diameter & Heat Output:** As mentioned earlier, a larger diameter rod generally delivers more heat. This is because a larger surface area means more material can be heated and melted. Think about it like this: imagine you’re trying to build a fire with a big log or a tiny kindling bunch. You need a decent amount of fuel for a big flame, right? The same principle applies in welding.
**Weld Penetration & Size:** A thicker rod will also provide more weld penetration, allowing it to penetrate deeply into the material and create stronger bonds. This is often critical when welding thick metals or during projects demanding robust welds.
**Weld Appearance:** Ultimately, rod diameter impacts how your finished weld looks: thicker rods offer a distinct “chunky” appearance while thinner ones produce smoother, more refined welds. The choice depends on your preference and the project at hand.
**Rod Diameter & Deposition Rate:** A thicker rod generally delivers higher deposition rates, meaning it melts and deposits metal faster. This can be beneficial for applications where speed is critical, such as welding large parts quickly or in high-volume production settings.
**Rod Diameter & Control:** Smaller diameters offer greater control over the weld pool, allowing for finer details and intricate designs. They enable welders to make precise adjustments for specific areas and achieve a more customized result.
Choosing the Right Rod: More Than Just Diameter
While rod diameter is an important factor, it’s not everything. Welding rods are more than just metal; they come with their own unique properties based on their composition and application:
**Electrodes & Materials:** The material of the electrode plays a crucial role in determining its welding capabilities: what kind of metals will you be working with? For instance, stick electrodes are great for steel, aluminum, and stainless steel. Tungsten Electrodes are best suited for high-temperature applications and high-speed welding.
**Gas Used:** Welding requires shielding gases to protect the weld pool from atmospheric contamination. These gases can also affect the arc’s characteristics and the resultant weld. Common options include Argon or Helium, each with unique properties that influence the weld’s bead appearance and penetration.
**Application & Specific Needs:** Every welding project has its own requirements; some might require higher levels of penetration while others prioritize a smooth finish. Consider these factors when choosing the right rods:
- **Type of metal being welded** (steel, aluminum, etc.)
- **Weld position and joint design** (flat, overhead, fillet welds, etc.)
- **Project’s desired end result** (smooth finish vs. heavy-duty weld)
Experiment & Learn
The best way to truly understand the impact of rod diameter is through hands-on experience. Experiment with different rod diameters on various metal types and settings to see how variations in their application affect your welding outcomes.
As your knowledge grows, you’ll learn to fine-tune your tig welding process based on the specific needs of each project. Remember that mastering this technique isn’t simply about selecting the “right” rod; it requires understanding the intricate dance between welder, metal, and power source.
**Remember:** The right rod is often a combination of its diameter, composition, and application. This knowledge translates into smoother welds, improved material penetration, and ultimately, a more fulfilling welding experience.