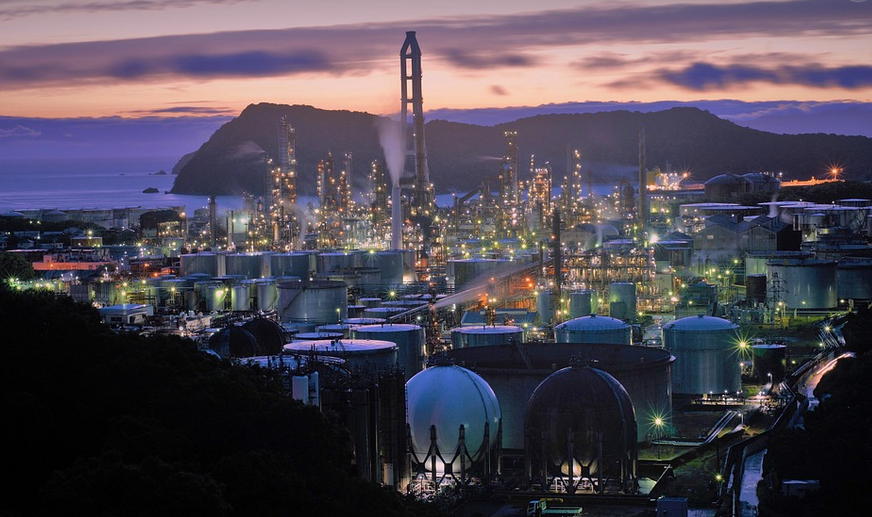
Thin Metal, Thick Skills: Tackling the Challenges
The world of welding is vast, offering an array of techniques and applications to suit various needs. One such technique, TIG welding, stands out for its precision and control, particularly when it comes to working with thin metal sheets. However, navigating the intricacies of TIG welding on delicate materials can feel daunting for beginners. But fear not! This comprehensive guide will demystify the process, equipping you with the knowledge and confidence to tackle your next thin metal project.
Let’s first dive into why TIG welding is particularly well-suited for thin metal sheets. TIG welding (also known as Gas Tungsten Arc Welding) offers unmatched control over the weld pool. The shielded arc produced by this method creates a highly localized and precise heat source, allowing for intricate and intricate geometries with minimal distortion. This makes it ideal for applications where precision and fine details are paramount.
Understanding the Tools of the Trade
Before diving into the actual welding process, understanding the key components of your TIG setup is crucial. Just like any other tool-dependent skill, proficiency in TIG welding depends on having the appropriate equipment. These include:
**1. The Torch:** This handheld device serves as the heart of your TIG rig. It houses a tungsten electrode that acts as the primary heat source for creating the arc. It’s essential to have a high-quality torch with a stable, reliable design and a precise control system.
**2. The Gas Supply:** TIG welding relies on shielding gas for optimal weld quality. This protective gas forms a shield around the molten metal droplets, preventing contamination from air and other unwanted elements. Common choices include argon or helium, each with unique characteristics that influence the weld’s stability.
**3. The Power Source:** Just like any electrical appliance, TIG welding needs electric power to operate. The power source provides the necessary voltage and current to ignite the tungsten electrode and create the arc. Opting for a stable and well-maintained power source is crucial for consistent and reliable weld quality.
Mastering the Fundamentals
Welding is about more than just wielding a torch; it’s about understanding its nuances. Before you begin welding, familiarize yourself with these core concepts:
**1. The Arc:** This is the heart of TIG welding. When the tungsten electrode touches the base metal and an electric arc forms between them, heat is generated, melting the base material and forming a weld pool.
**2. Preheating:** Before welding thin metals, especially if they are prone to distortion, preheating the metal can help mitigate this issue. This involves raising the temperature of the base piece slightly above room temperature to reduce its thermal stresses during welding.
**3. Shielding Gas Flow:** The choice of shielding gas and its flow rate affects the weld pool’s stability and penetration. When using argon or helium, proper flow control ensures clean and free-from-contamination welds.
Tacking: The Art of Prepping for Success
Tack welding comes before the main welding process. It’s like a preliminary “handshake” between two pieces of metal, helping them stay securely aligned during final welding.
**Why Tack?** Tack welding ensures clean cuts and precise alignment. The small welds serve as temporary anchors, holding the pieces together for further fusion. This is especially important when working with thin metal sheets where slight misalignment can lead to significant distortions.
**How to Tack:** Use a low-heat setting on your TIG torch and create a short, focused weld between two adjacent edges of your metal sheet. Keep the welding time minimal, ensuring only a shallow penetration is achieved. This will prevent excessive heat transfer from the torch and reduce warping.
Welding Technique: Precision in every Pass
A Few Tips to Remember:**
* **Follow the Weld Path:** Start by using a smooth, controlled arc travel path. This ensures uniform weld bead formation. * **Pre-Heat for Distortion Control**: If necessary, preheat thin metals before welding to minimize distortion and warping. * **Weld Slowly:** Welding too quickly can create uneven welds, leading to gaps or incomplete penetration. Take your time and work carefully at a steady pace. * **Don’t Overload the Torch:** The heat generated by TIG welding should be controlled. Avoid holding the torch for extended periods, which may cause overheating and potential damage to the metal.
Safety First: Always Prioritize
Working safely is paramount in welding. Here are some essential safety precautions: * **Eye Protection:** Wear appropriate eye protection (e.g., welding goggles) at all times to shield your eyes from splatter and any flying debris. * **Welding Gloves:** Protect your hands with heavy-duty welding gloves, which offer superior heat resistance and dexterity.
**Ventilation:** Ensure adequate ventilation in the workspace, especially when using gas shielding gases. This prevents harmful fumes and gases from building up to dangerous levels.
Learning From Experience
TIG welding thin metal is a continuous learning process. Embrace every challenge as an opportunity for growth!
**Practice, Practice, Practice:** The more you weld, the better you’ll become at controlling your torch and maintaining consistent weld quality.
**Experiment with Different Metals:** Explore various metals and see how their properties affect the welding process
Final Thoughts: Your Welding Journey Begins
TIG welding thin metal has a unique charm, demanding careful attention to detail. With each project, you’ll hone your skills, gain confidence, and develop a deeper understanding of this valuable welding technique. Congratulations on embarking on this exciting journey!
Remember, the key is a steady hand, meticulous precision, and a commitment to safety.