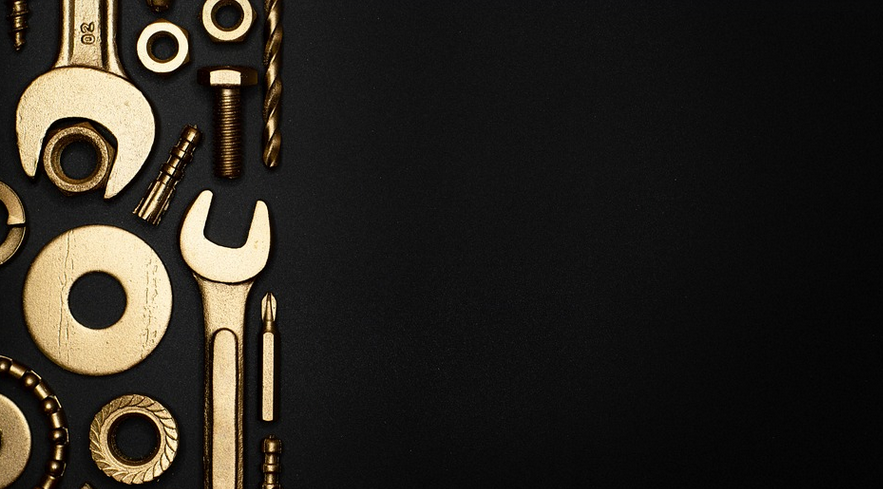
Understanding the Importance of Welding Gases
Welding, in its essence, is a delicate dance between heat and metal. It’s about melting molten metal together by applying controlled heat, often using specialized gases. These gases play a vital role in the welding process, influencing everything from weld quality to safety. Choosing the right welding gas can make all the difference in achieving a strong, lasting weld.
Welding gases act as shields and facilitators during the welding process, creating ideal conditions for successful metal joining. They react with the molten metal, forming an inert atmosphere that prevents oxidation and improves the welding torch’s performance. Understanding the different types of gases is crucial to ensuring optimal results and safety on any welding project.
The most common type of welding gas is **shielding gas**, the cornerstone of many welding processes. It’s the shield against harmful elements like oxygen and nitrogen that can react with the molten metal and create weak welds or even a fire hazard. Common shielding gases include:
Shielding Gases Explained
**Argon (Ar):** The workhorse of welding, argon is a non-reactive gas known for its excellent ability to protect weld pools from oxygen contamination. It’s commonly used in MIG, TIG and SMAW welding processes. Argon also acts as a filler material, reducing slag formation and ensuring a smooth weld bead.
**Helium (He):** This inert gas is lighter than argon but still offers exceptional shielding capabilities. It’s often added to the mix during TIG welding where it improves arc stability and reduces spatter. Helium also helps with bead control, creating more consistent weld beads.
**Mix of Argon & Others:** Shielding gases are not always just one type! Sometimes, a blend of different gases is used for specific applications. For example, 95% argon and 5% helium is often preferred for welding stainless steel due to its ability to prevent porosity and ensure uniform weld bead formation.
**Beyond Shielding Gases:** Besides shielding gases, there are other gas types used in welding projects:
Other Welding Gas Types
**Coverage Gases:** These gases create a protective environment around the weld zone, preventing oxidation. They’re often used when dealing with thick metals and high temperatures. Examples include:
- **Carbon Dioxide (CO2):** This gas is known for its ability to produce a strong fume shield during welding processes like oxy-fuel welding and cutting.
- **Methane (CH4):** Mostly used in cutting applications, it’s also employed as the shielding gas in certain welding practices. It creates a dense atmosphere that prevents oxidation and ensures clean welds.
**Specific Gas Applications:**
Gas Selection: Know Your Project and Weld Style
Choosing the right welding gas depends on several factors, including your specific welding process, application, and desired weld quality. You might be wondering about the different welding styles and why the specific gases are important for each one:
**MIG (Metal Inert Gas):** Commonly used in various industries due to its versatility, MIG welding utilizes a continuous wire electrode fed into the welding zone alongside shielding gas. Commonly used with **Argon or a 50/50 mix of Argon and CO2.**
**TIG (Tungsten Inert Gas):** Typically used for precision applications where high control and weld quality are desired. TIG welding uses a non-consumable tungsten electrode and shielding gas. It’s known for its superior control over the weld pool, leading to more accurate welds.
**SMAW (Shielded Metal Arc Welding):** Also known as stick welding, it employs electrodes coated with flux that protect the weld pool from atmospheric contamination. It utilizes a variety of shielding gases like **Argon or CO2 and sometimes a mixture of both**.
**Other Factors to Consider:**
Beyond these common types of welding gas, there are specialized gases for specific applications:
- **Oxy-fuel Welding Gases:** These gases provide the necessary oxygen to generate intense heat and melt metals during oxy-fuel cutting and welding.
- **Specialty Gases:** Used in specialized applications like laser welding, where different types of gas mixtures are required to control the arc and achieve desired results.
Understanding the nuances of these gases helps you choose the right one for your specific project.
Safety First: Always Follow Guidelines
Choosing the right welding gas is only part of the equation. Welding, by its very nature, involves hazards that require strict safety precautions. Remember:
- **Always work in a well-ventilated area:** Welding gases release harmful fumes and pollutants into your workspace.
- **Wear proper protective gear:** This includes welding helmets, gloves, respiratory masks, and clothing to protect yourself from fire hazards, burns, and other potential injuries.
- **Use the correct equipment and materials:** Ensure you have the appropriate equipment for the type of gas used and follow manufacturer guidelines.
Welding processes require a deep understanding of safety rules and procedures. It’s crucial to stay informed about the specific hazards associated with each welding process and take necessary precautions to ensure your safety.