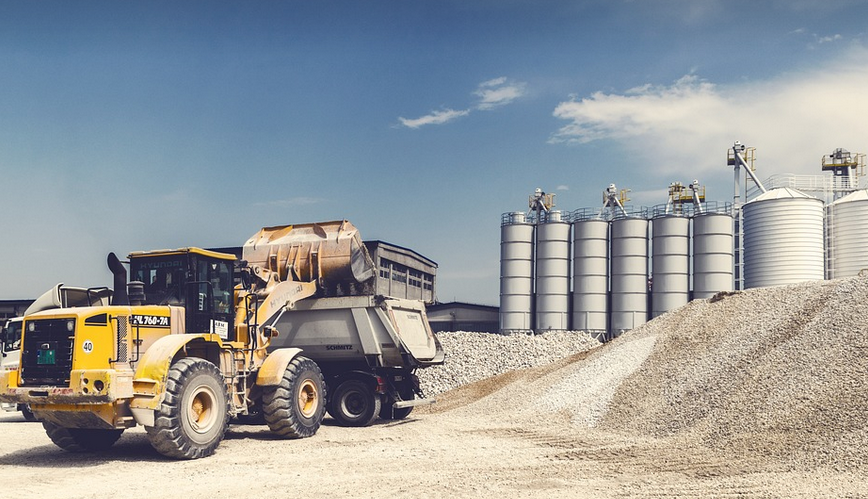
The Power of Welding Skids on the Road
A welding skid is a versatile and essential piece of equipment designed to enhance the capabilities and safety of trucks in various industries. From construction and transportation to maintenance and repair, these skids offer a crucial combination of portability, functionality, and adaptability. A well-designed welding skid can be an invaluable asset for any fleet owner or operator, boosting efficiency, safety, and overall productivity.
Imagine hauling heavy equipment like cranes, forklifts, or even trailers. Having a dedicated platform with the tools you need right at your disposal simplifies tasks, reduces downtime, and minimizes potential injury risks.
Welding skids are essentially portable workspaces designed to provide a secure and stable platform for welding activities. They allow mechanics to perform repairs and modifications on-site, eliminating the need for cumbersome setups or specialized equipment. This streamlined approach offers numerous advantages: Increased productivity, enhanced safety, optimal workspace organization, and cost-efficiency.
Understanding the Benefits of Welding Skids
The impact of welding skids extends beyond just functionality; their benefits are woven into the fabric of modern work practices:
**1. Increased Productivity:** The versatility of a welding skid allows for quick and easy setup, freeing up valuable time and labor that can be allocated to other tasks.
**2. Enhanced Safety:** Welding skids come equipped with safety features such as built-in handrails and guard rails, ensuring a secure working environment and minimizing the risk of accidents or injuries.
**3. Optimized Workspace:** Dedicated space for welding materials, tools, and equipment eliminates clutter and promotes a more organized work area.
**4. Cost-Efficiency:** By reducing the need for travel time to service centers and eliminating potential delays caused by transportation issues, welding skids offer significant cost savings in the long run.
**5. Increased Flexibility:** Welding skids can be easily transported and deployed to different locations, making them a valuable tool for businesses with diverse operations.
With proper design and maintenance, welding skids become far more than just transport platforms; they evolve into efficient workspaces that enhance productivity and safety on the road.
What Makes a Welding Skid Special?
A well-designed welding skid is much more than just a platform. It’s a carefully engineered combination of different components, each playing a crucial role in its overall functionality:
**1. Strong and Durable Construction:** The foundation of any successful welding skid lies in its structural integrity. Materials like steel or aluminum are chosen for their resilience and resistance to wear and tear.
**2. Secure Platform:** Ensuring a stable work platform is paramount, allowing mechanics to perform tasks confidently without fear of accidents. This often involves robust frame designs with sturdy legs that can support heavy machinery.
**3. Efficient Tool Storage:** Dedicated compartments for welding equipment like torches, wire feeders, and cables allow for easy access while minimizing clutter and potential hazards.
**4. Precise Tooling:** Welding skids often incorporate specialized tooling like clamps, welders’ stands, and work lights to ensure optimal performance and safety during tasks.
**5. Safety Features:** To boost the overall safety of welding operations, welding skids are equipped with features such as emergency brakes, handrails, and fire suppression systems that minimize risks and safeguard workers.
These carefully engineered components work together to create a robust and reliable platform for welding activities, optimizing efficiency and ensuring worker safety on the go.
Welding Skids: The Future of Fleet Management
The evolution of welding skids continues to shape fleet management. New technologies and advancements are constantly being developed that promise enhanced functionality, even greater efficiency, and improved sustainability.
Some key trends include:
- **Automation:** Integrated robotic systems for tasks like arc welding or spot welding are becoming increasingly common, contributing to increased productivity and reduced human error.
- **Sustainable Materials:** Shifting towards eco-friendly materials like recycled metals and lighter-weight construction techniques is becoming a priority in the industry.
- **Smart Technologies:** Improved connectivity with data analysis tools allows fleet managers to monitor their skids’ performance, predict maintenance needs, and optimize operations for greater efficiency.
As these trends continue to develop, welding skids will become even more sophisticated and effective, paving the way for a new era of streamlined and efficient work practices across various industries.
Investing in high-quality welding skids is no longer just about practicality; it’s about building a more efficient, safer, and ultimately, stronger fleet. The future of mobile welding operations lies in a well-designed and carefully maintained skid, ready to face any challenge on the road.