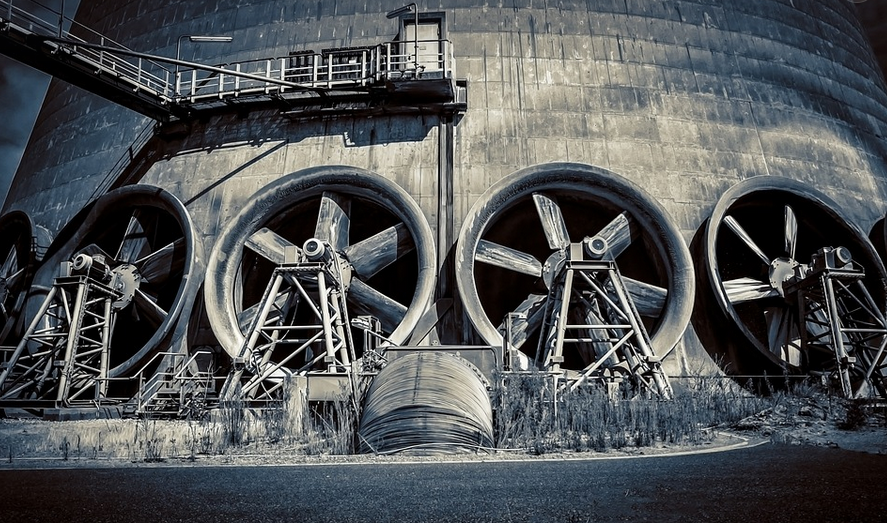
What are Welding Stingers and Lead?
Welding stinger leads, also known as “lead” or “stinger cables,” are essential components in arc welding. They’re more than just a bunch of wires; they represent the heart of how we generate power in this process. Think about it like this: a stinger is basically a cable that conducts electricity from your welding machine to the welding torch, allowing you to create sparks and melt metals together!
Understanding Welding Dynamics
Before we dive into stingers, let’s take a moment to appreciate the magic of arc welding. It’s all about creating an electric arc between two electrodes – one held by the welder, the other positioned by the workpiece itself. This controlled “electrical spark” melts the base metal, allowing it to fuse together with whatever you’re working on.
The Role of Stingers in Arc Welding
Stingers are crucial in this process for several reasons: * **Power Delivery:** The stinger transfers power from your welding machine to the torch. Imagine a water pipe – the stinger is like that pipe! It carries the electricity, and without it, there would be no flow! * **Electrode Connection:** Welding requires precise control over the flow of electric current. Stingers help create this controlled environment by connecting the electrodes in the correct way to ensure reliable arc generation.
Types of Stingers: A Spectrum of Options
Stinger cables come in various forms, each optimized for specific applications and environments: * **Shielded Cables:** In welding, a shield is essential! Shielded stinger cables have an added layer of insulation called “shielding gas.” This layer protects the welding area from unwanted sparks and fumes, creating a cleaner, safer environment. * **Non-Shielded Cables:** These cables are perfect for situations where shielding is not necessary due to limited exposure to sparks and fumes. They offer flexibility and cost-effectiveness in these circumstances.
Lead Wire: The Bridge Between Stinger and Torch
The term “lead” often gets used interchangeably with “stinger,” and rightfully so! Both terms refer to the wires that bridge the gap between the welding machine’s power source and the welding torch. They ensure a smooth flow of electric current, forming the foundation for creating a successful weld. Think about it this way, lead wires are like little bridges connecting the ground (earth) to your welding machine!
The Power Behind the Stinger: Understanding Voltage
Voltage is the force that drives electricity to do work. It’s measured in volts (V). In arc welding, think of voltage as the “pressure” behind the stinger; it’s what helps the current flow smoothly and efficiently through your machine!
Choosing the Right Lead/Stinger: Factors to Consider
Selecting the perfect lead or stinger for your project involves more than just choosing a wire. It’s about understanding your welding needs, welding equipment, and environment. * **Voltage Requirements:** The power output of your welding machine dictates the voltage you need in your stingers. * **Amperage Considerations:** This refers to the amount of current flowing through the stinger. You need to know how much current your welding machine can handle before even starting to choose a lead!
Safety First: Working with Stingers and Leads
Working with electricity always carries risk, so it’s crucial to prioritize safety when dealing with welding leads and stingers: * **Proper Handling:** Always handle stinger cables with care, as they run on high voltage. Never touch the exposed ends of these wires! Use gloves to protect yourself from accidental shocks or burns. * **Grounding Safety:** Always ensure your welding area is grounded properly before operating your welding machine. This prevents electrical hazards and ensures a safe working environment.
Maintenance and Longevity: Keeping Your Stingers in Top Condition
Proper maintenance can significantly extend the life of your stingers: * **Regular Cleaning:** Make sure to clean your stinger cables after each use to remove dust, dirt, or debris that can block the flow of electricity. This prevents corrosion and keeps your wires performing optimally for a longer time! * **Inspection Before Use:** Every time you get ready to use a stinger, it’s essential to check its condition. Look for any signs of damage like fraying, cuts, or breaks in the wires themselves. **Conclusion: The Power Behind Welding** Welding stingers and lead are critical components that enable arc welding to work its magic! From transferring power to creating a controlled electric arc between electrodes, these components play crucial roles. Choosing the right stinger and lead, understanding their functions, and prioritizing safety is essential for successful welding projects. By taking care of your welding equipment, you’ll ensure years of reliable performance and safe welding experiences.