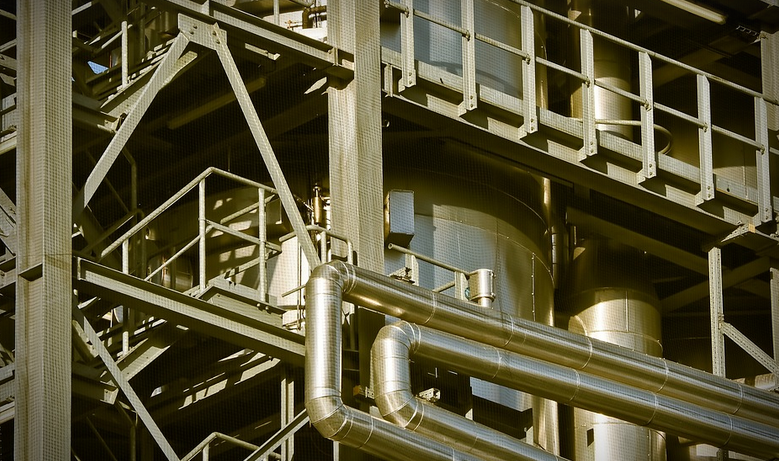
Understanding the Basics
Aluminum welding rods, specifically those made from cast aluminum alloys, hold a unique place in the welding industry. Their versatility and advantages make them popular for various applications, ranging from lightweight structural components to intricate machinery.
The Anatomy of Cast Aluminum Welding Rods
Cast aluminum welding rods are distinct due to their construction. They consist of a central rod with an alloy coating designed for controlled weld penetration. These rods come in different diameters, each tailored for specific application needs. Understanding the diameter is crucial since it determines the amount of material being added during the welding process.
Cast aluminum rods are also categorized based on their melting points or solidifying temperatures. This categorization allows welders to select the appropriate rod for the job, ensuring optimum performance and weld quality. Choosing a rod that matches the application prevents unwanted variations in weld properties and ensures consistent results.
Why Cast Aluminum Welding Rods?
The popularity of cast aluminum welding rods stems from their versatility and ability to deliver high-quality welds. They are ideal for both manual and automatic welding processes, making them suitable for a wide range of projects.
Cast aluminum welding rods offer several advantages over other types of welding rods:
* **Precision Welding:** The precision of cast aluminum welding rods allows for intricate welds on small parts. Their controlled melting point and solidification properties enable precise control during the weld process, leading to stronger and more consistent welds than those made with traditional welding methods.
**Versatility in Material Thickness:** Cast aluminum welding rods are suitable for welding thin materials, thanks to their controlled melting point. This makes them a preferred choice for applications where precision and control over the weld thickness is crucial.
Applications of Cast Aluminum Welding Rods
Cast aluminum welding rods find their use in various industrial sectors due to their versatility. Here are some common applications:
- * **Aerospace Industry:** Their lightweight and strength-to-weight ratio make them ideal for aircraft structures, engine components, and other aerospace applications. * **Automotive Industry:** Cast aluminum welding rods find use in various automotive vehicles, including chassis components, engine blocks, and transmission housings. These rods’ ability to withstand heat and pressure makes them a reliable choice for demanding automotive applications. * **Marine Industry:** Cast aluminum welding rods prove valuable for constructing marine vessels, including hulls, decks, and structural components due to their corrosion resistance.
* **Construction Industry:** Cast aluminum welding rods are widely used in the construction industry. Their ability to form strong bonds with various materials makes them suitable for creating bridges, buildings, and other infrastructures.
These applications highlight the versatility of cast aluminum welding rods across diverse industries.
Safety Precautions When Welding
Welding any metal presents safety risks; however, precautions can be taken to minimize them. Safety should always be prioritized when working with metals and using welding equipment:
- * **Personal Protective Equipment (PPE):** Always wear appropriate PPE while welding, including: welding helmets, leather gloves, and protective clothing to prevent burns and other hazards.
* **Ventilation:** Ensure adequate ventilation in the workspace. Welding fumes can be harmful; it’s crucial to keep air circulating properly to avoid inhaling potentially harmful substances.
* **Electrical Safety:** Ensure all electrical wiring is properly grounded and maintained. Avoid overloading circuits or using damaged cords. These precautions help prevent electrical hazards that could lead to a fire or electric shock.
Looking Ahead: The Future of Cast Aluminum Welding Rods
Cast aluminum welding rods continue to evolve, with advancements in materials science and process optimization. New materials and welding technologies are continually being developed to enhance the performance and efficiency of these welding rods:
**Improved Welding Performance:** Research is ongoing to develop even more efficient and precise cast aluminum welding rods. These developments aim to improve weld quality, reduce heat input during the fabrication process, and increase productivity for welders.
**Sustainability in Manufacturing:** The production of cast aluminum welding rods is constantly being streamlined and optimized to minimize its environmental impact. This includes adopting more sustainable manufacturing methods and using recycled materials where possible.
Conclusion
Cast aluminum welding rods have earned their place in the welding industry due to their versatility, precision, and durability. These rods offer a reliable solution for various applications, ranging from aerospace to construction. Their ability to deliver high-quality welds with precision makes them an essential tool for many industries.